Ecotherm's Skived Heat Sink
Skived heat sinks represent an efficient cooling technology widely used across various domains, particularly excelling in applications with limited space and high airflow requirements. This article delves into the working principles of skived heat sinks, their manufacturing processes, and their applications in different sectors.
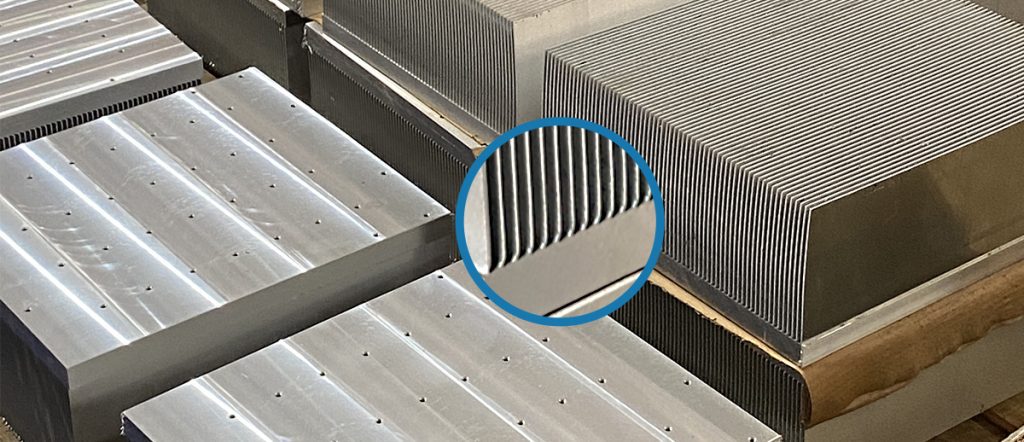
Skived Heat Sink Advancements:
- Increased Surface Area:Skived heat sinks are crafted from thermally conductive materials, typically copper or aluminum, into thin and densely packed fin-like structures. This design significantly increases the heat sink’s surface area. Compared to traditional heat sinks, skived heat sinks provide more surface area for rapid heat dissipation into the surrounding environment.
- Material Selection:Skived heat sinks often utilize copper or aluminum. Copper boasts excellent thermal conductivity, with a thermal conductivity coefficient as high as 398 (W/(m·K)), making it an outstanding choice for heat conduction. Aluminum, while slightly inferior to copper in thermal conductivity with a coefficient of 237 (W/(m·K)), offers advantages such as lighter weight and lower cost, making it a common heat sink material in certain applications. The choice of material depends on specific heat dissipation design requirements and constraints, and Ecotherm provides tailored recommendations.
- Customized Design:Ecotherm offers customization services, allowing adjustments to fin size, thickness, height, and the number of fins to match specific application requirements. This personalized design ensures that skived heat sinks perfectly cater to the demands of particular applications, providing optimal heat dissipation performance.

Increased Surface Area
Skived heat sinks are crafted from thermally conductive materials, typically copper or aluminum, into thin and densely packed fin-like structures.
This design significantly increases the heat sink’s surface area.
Compared to traditional heat sinks, skived heat sinks provide more surface area for rapid heat dissipation into the surrounding environment.
Material Selection:
Skived heat sinks often utilize copper or aluminum.
Copper boasts excellent thermal conductivity, with a thermal conductivity coefficient as high as 398 (W/(m·K)), making it an outstanding choice for heat conduction.
Aluminum, while slightly inferior to copper in thermal conductivity with a coefficient of 237 (W/(m·K)), offers advantages such as lighter weight and lower cost, making it a common heat sink material in certain applications.
The choice of material depends on specific heat dissipation design requirements and constraints, and Ecotherm provides tailored recommendations.
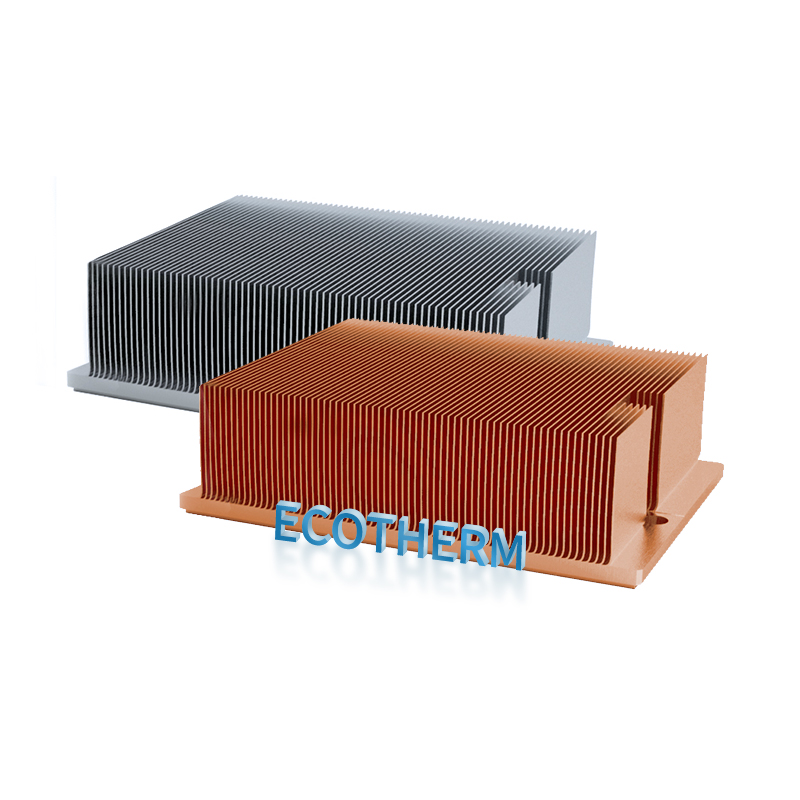
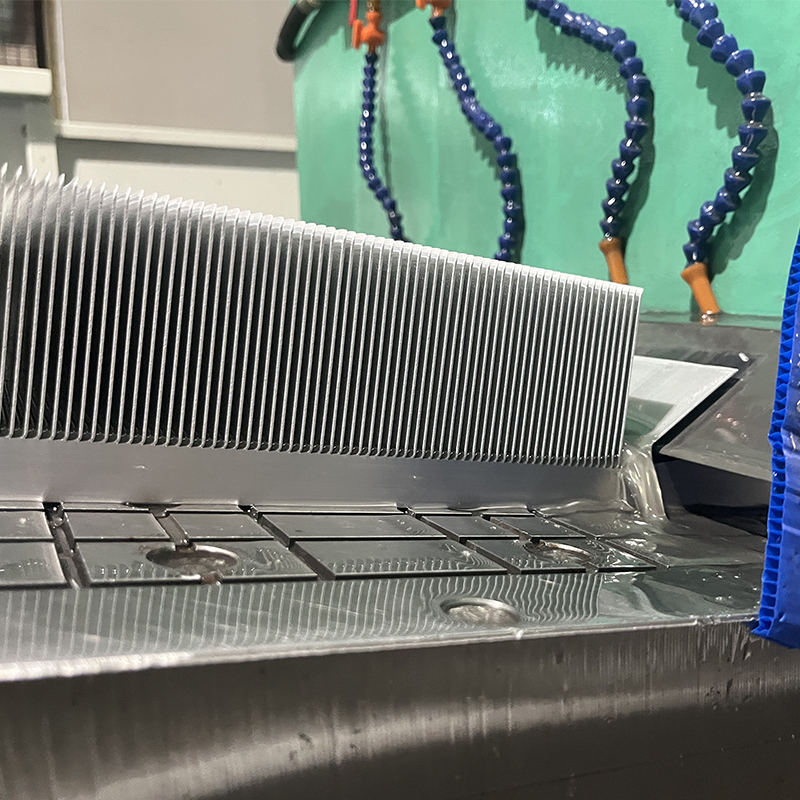
Customized Design
Skived heat sinks are crafted from thermally conductive materials, typically copper or aluminum, into thin and densely packed fin-like structures.
This design significantly increases the heat sink’s surface area.
Compared to traditional heat sinks, skived heat sinks provide more surface area for rapid heat dissipation into the surrounding environment.
Manufacturing Process of Skived Heat Sink
-
Engineering Consultation:
Initially, customer requirements are discussed to determine their heat dissipation needs. Ecotherm’s engineers assess these requirements and provide technical recommendations, including optimal material selection, heat sink design, groove density, and other aspects.
-
Sample Fabrication:
Typically, one or more samples are fabricated for customer testing. These samples are manufactured to design specifications to ensure their performance and appearance meet requirements. Customer feedback and approval are crucial for the successful production of the final product.
-
Mass Production:
Once sample feasibility is confirmed by the customer, Ecotherm initiates mass production of heat sinks according to approved samples and design specifications. This process involves multiple steps such as material cutting, heating, rolling, cooling, cutting, shaping, surface treatment, and more, ensuring the quality and performance of each heat sink meet requirements.
-
Quality Control:
The manufacturer conducts quality control and testing for each heat sink to ensure their performance and quality meet high standards, guaranteeing the reliability and stability of the final product.
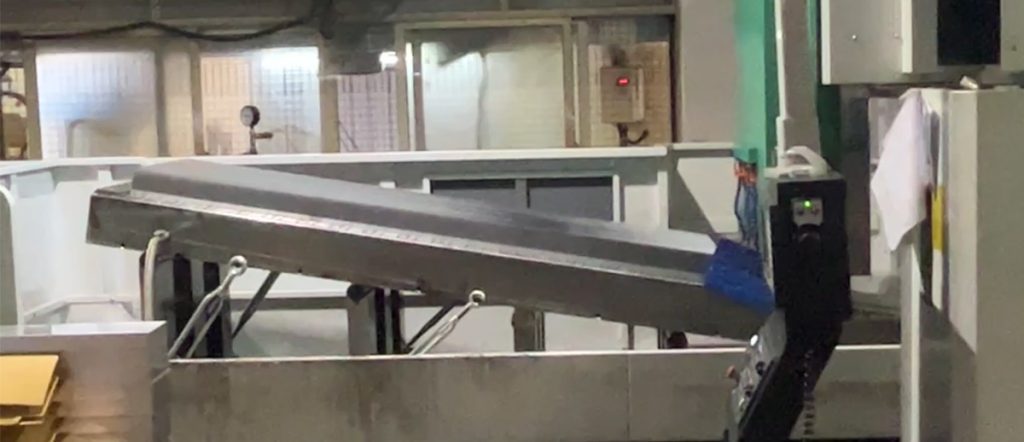
Advantages of Skived Heat Sink
Skived heat sinks offer a range of advantages, including but not limited to:
- Efficient Heat Dissipation Performance
- Cost-effectiveness
- Thin and dense fin design suitable for compact spaces
- Integration with heat pipes for enhanced performance
- Surface treatments available to extend lifespan
Skived heat sinks are widely embraced due to their efficient heat dissipation capabilities and customization options.
Process parameters:
Skived heat sinks offer a range of advantages, including but not limited to:
Skived heat sinks are widely embraced due to their efficient heat dissipation capabilities and customization options.
Material | Fin Thickness | Width | Length | Fin Heigh | Fin Pitch |
---|---|---|---|---|---|
Copper | 0.1-1mm | ≤900mm | ≤3000mm | ≤80mm | 0.16-12mm |
Aluminum | 0.2-2mm | ≤900mm | ≤3000mm | ≤130mm | 0.2-12mm |
Some typical application areas include:
Electronic Devices:
Cooling for computers, servers, and power supplies.
LED Lighting:
Enhancing the heat dissipation of LED fixtures to extend their lifespan.
Power and Electronics Modules:
Integrating heat sinks into modules like power supplies, inverters, and amplifiers to improve heat dissipation efficiency.
Communication Equipment:
Ensuring stable and reliable heat dissipation for wireless communication devices, base stations, and network equipment.
Electric Vehicles:
Managing the temperature of battery management systems and motor controllers in electric vehicles.
Conclusion
Skived heat sink, as an efficient heat dissipation technology, not only delivers outstanding cooling performance but also offers extensive customization capabilities to meet the diverse requirements of various application fields. Its unique design principles, including increased surface area, flexible material selection, and customization options, make it an ideal choice for addressing multiple heat management challenges.
With the continuous advancement of modern technology and the increasing demand for high-performance electronic devices and other heat-sensitive systems, the role of skived heat sinks becomes increasingly critical. Their widespread use in electronics, LED lighting, power modules, communication equipment, electric vehicles, and medical devices provides reliable solutions for industries across the board.
Ecotherm remains committed to providing high-quality Skived heat sink products to its customers and actively participating in heat management challenges across diverse application fields. Whether it’s meeting efficiency requirements, reducing costs, or enhancing system stability, Skived heat sinks will continue to play a pivotal role in heat management, driving technological innovation and development.
If you have further questions or requirements regarding Skived heat sinks or other heat dissipation technologies, please feel free to contact us. We are dedicated to providing professional technical support and solutions. Thank you for reading this article, and we look forward to assisting with your heat dissipation needs!