Liquid cold plate/water cooling block
Water-cooling plate is a crucial component in the cooling system.
The manufacturing process of liquid cooling plates is much more complex than that of air-cooled heat sinks.
Generally, liquid cooling plate production technologies include buried pipe technology, profile + welding, machining + welding, and die casting + welding.
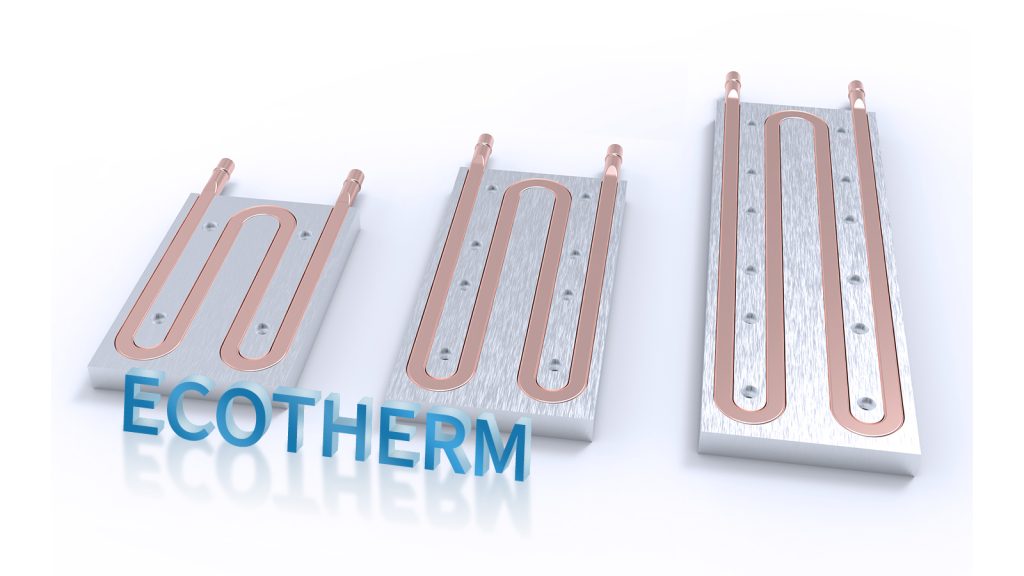
Buried Pipe Technology:
Buried pipe technology is the most commonly used manufacturing process for liquid cooling plates in liquid coolers. Typically, it involves embedding copper pipes in aluminum substrates. The process includes CNC machining of grooves on the aluminum substrate, followed by pressing pre-bent copper pipes onto the substrate using a stamping machine. After that, brazing is performed, and further processing results in the water-cooling plate.
This technology has four variations: shallow buried pipe, deep buried pipe, welding pipe, and double-sided clamping pipe.
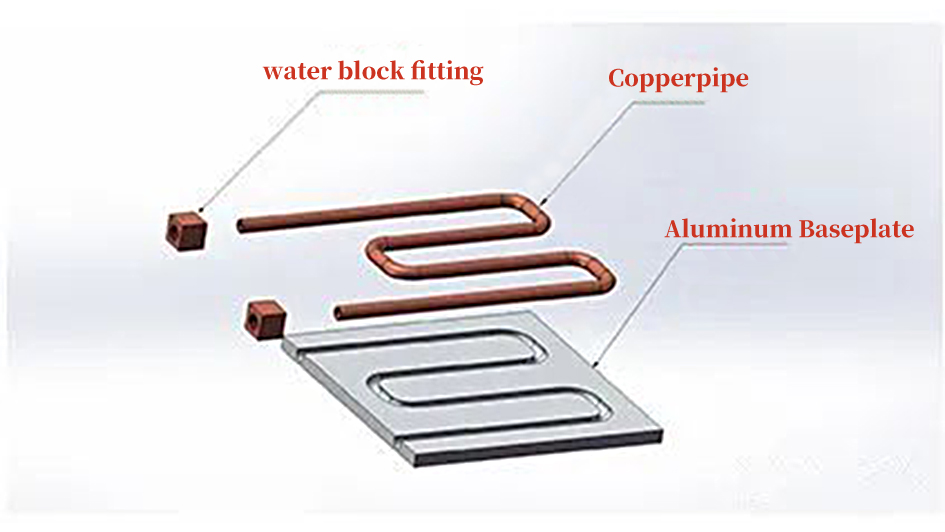
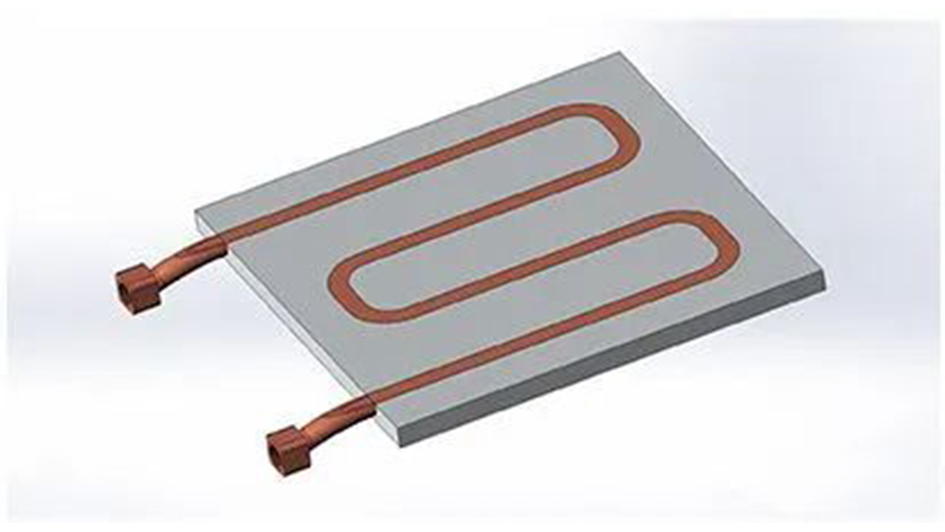
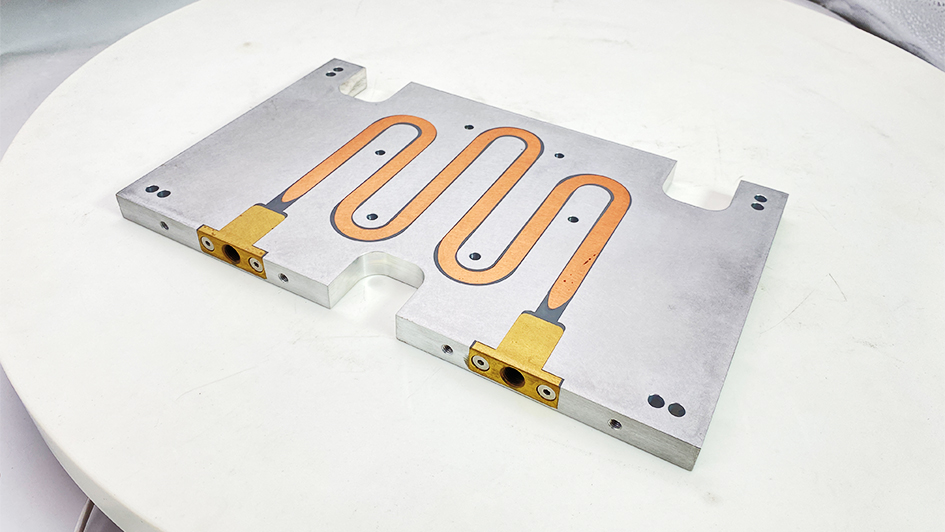
Shallow buried pipe
involves flattening the copper pipe and milling the surface of the aluminum plate simultaneously, taking advantage of the high thermal conductivity of the copper pipe to dissipate heat and utilizing the lightweight nature of aluminum for weight reduction and cost control.
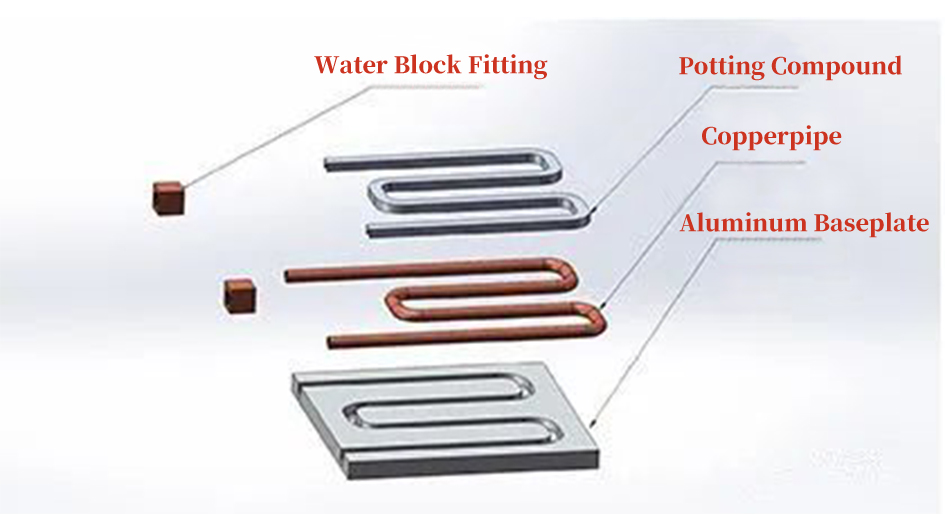
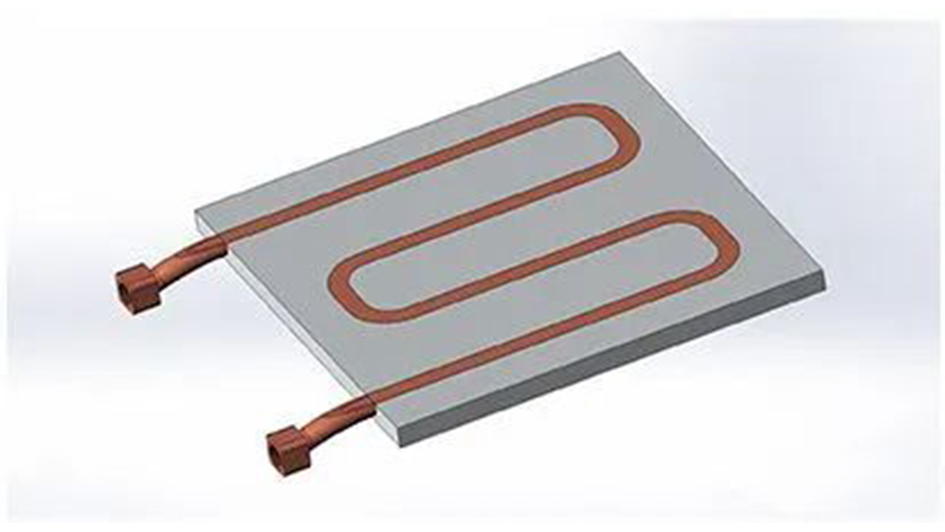
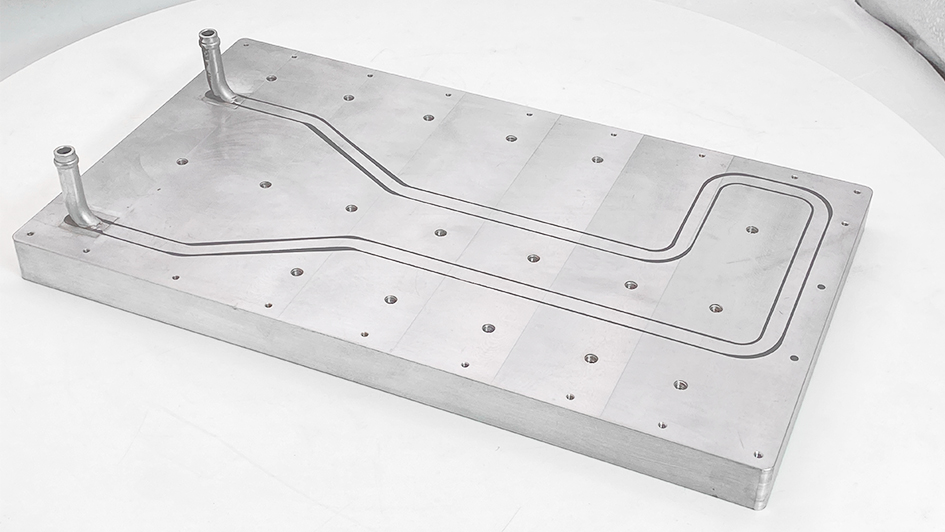
Deep buried pipe
technology uses high thermal conductivity epoxy resin as filler. It is suitable for applications where the cooling device’s temperature difference requirements are not high. It can be installed on both sides, and the thickness of the copper pipe is not subjected to secondary processing. The filler provides protection, ensuring safety, making it particularly suitable for cold plates using refrigerants as the medium.
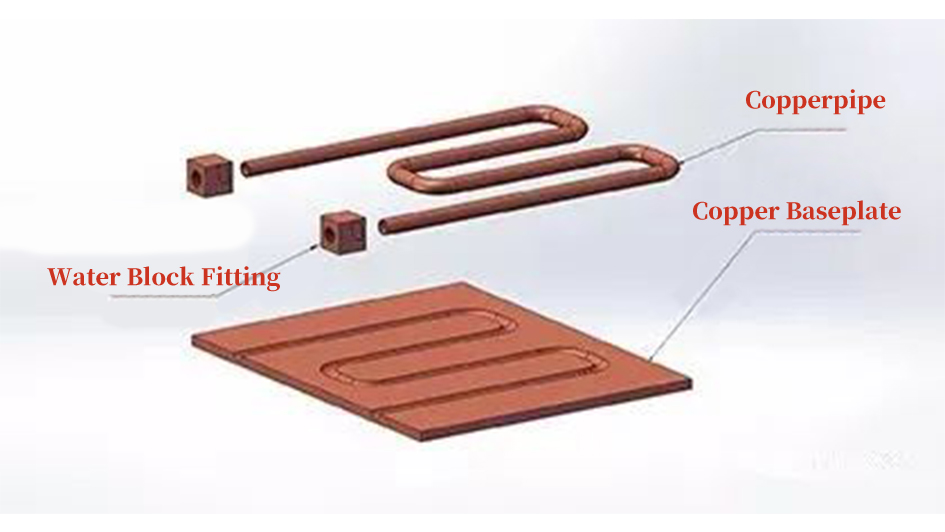
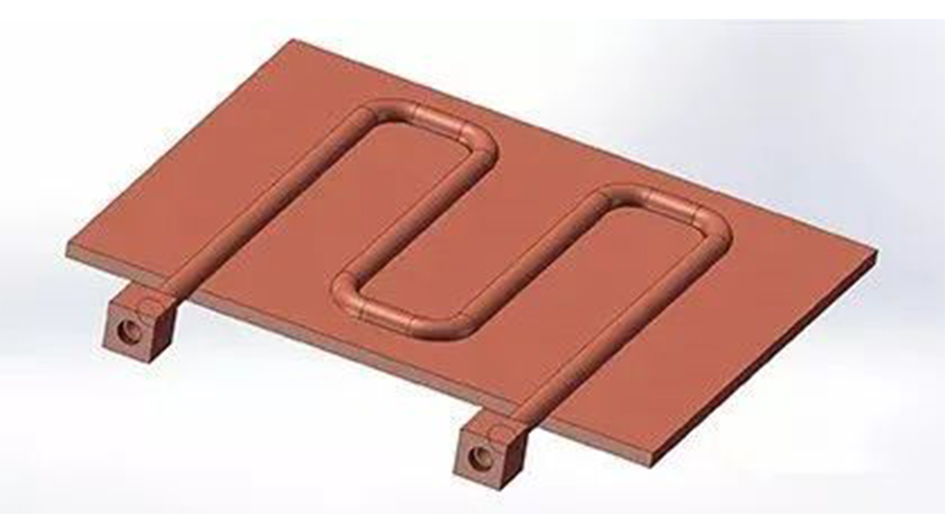
Welding pipe technology
involves directly welding the heat pipe to the base plate.
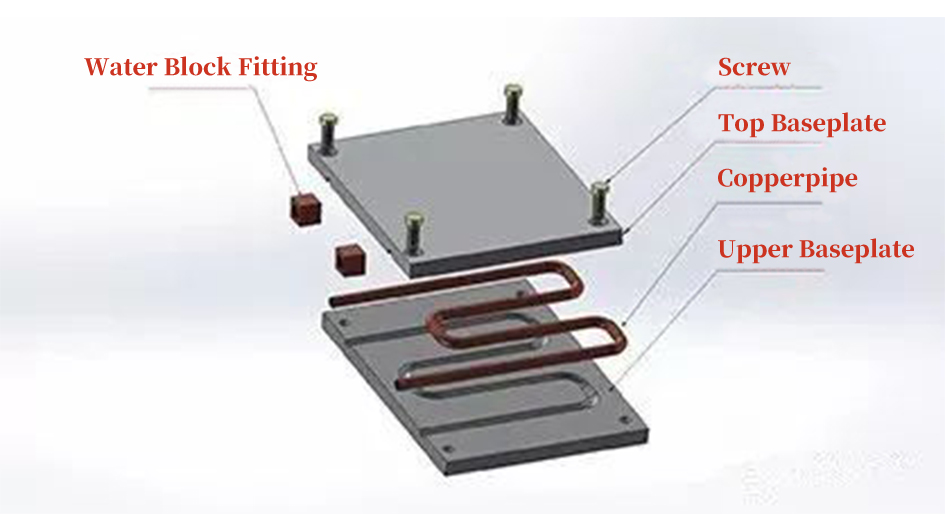
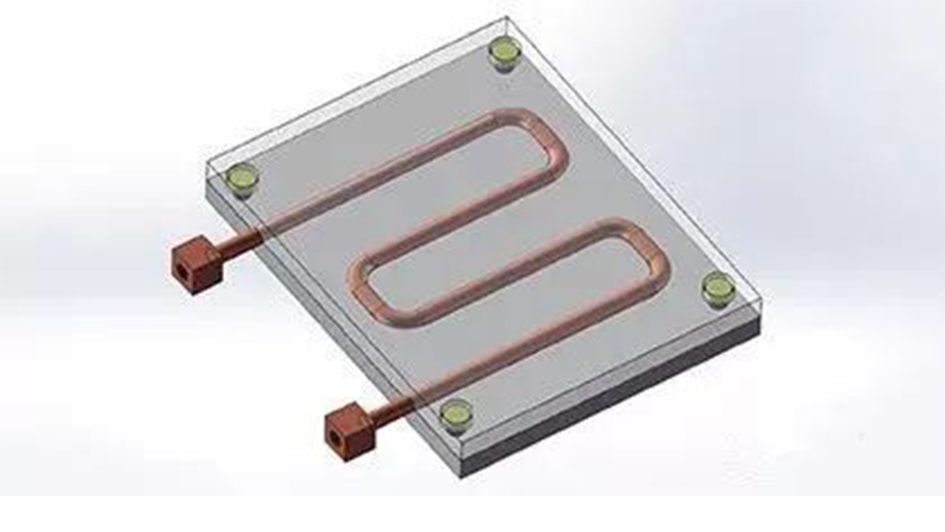
Double-sided clamping pipe technology
uses screws to fix the upper and lower base plates, clamping the heat pipe in the middle.
Profile + Welding:
In the process of manufacturing liquid coolers, various shapes, including plate type, channel type, and combination type, are achieved through profile processing. The entire production process is based on the processing and welding of profiles, combining profiles with joint pipelines to form the overall liquid cooler.
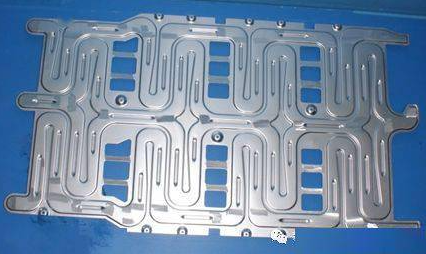
Through extrusion, the cooling plate channels are directly formed, followed by machining to establish circulation. In terms of sealing, friction welding and brazing processes are used to ensure efficient sealing while maintaining relatively low costs. However, this method is not suitable for applications with high heat dissipation density or situations with excessive surface screw holes, restricted waterway directions, or reduced reliability.
This process is mainly applied to power battery water-cooling heating devices, water distribution boxes, and integrated cooling products for standard power modules.
Machining + Welding:
The production of water-cooling plates involves machining, allowing for the free design of internal channel sizes and paths. This method is particularly suitable for heat management products with high power density, irregular heat source layouts, and limited space. Its main application areas include wind power inverters, photovoltaic inverters, IGBTs, motor controllers, lasers, energy storage power supplies, supercomputing servers, etc. However, its application in power battery systems is relatively limited.

Microchannel coolers are also a type of cooler manufactured using a combination of machining and welding processes. The production of this cooler is relatively complex and is suitable for machines with high heat dissipation power and a concentrated distribution. The wide and uniform channels of microchannels can quickly dissipate concentrated heat. However, the manufacturing process of microchannel liquid coolers is complex, often requiring machining of microchannels and then welding through friction welding processes, resulting in relatively high manufacturing costs.
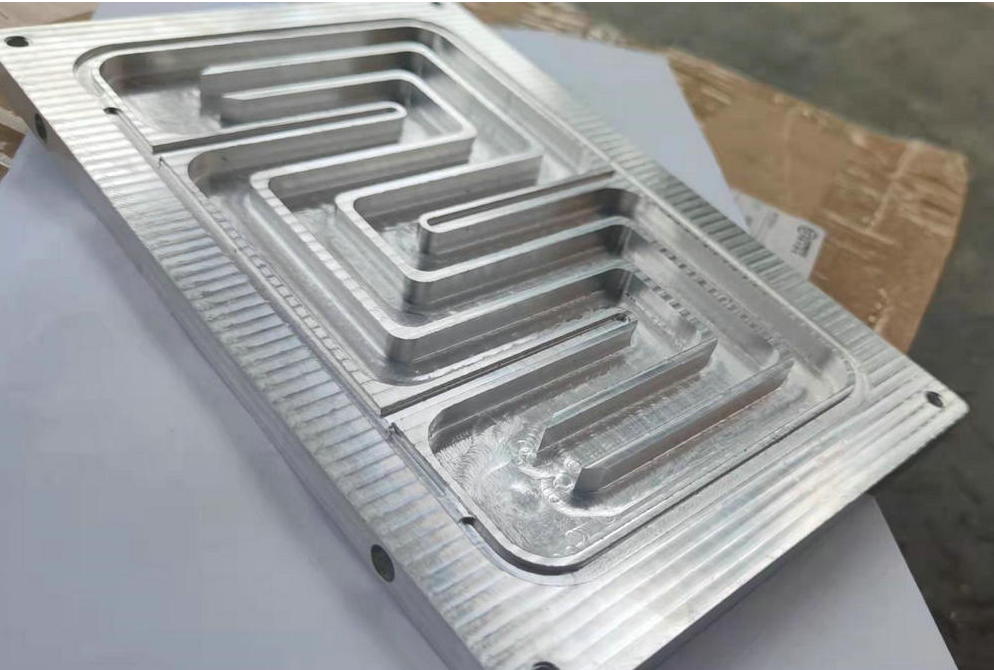
Die Casting + Welding:
Die casting is a mature and widely used molding method, extensively adopted in the rapid development of new energy vehicles. Die-cast molding is the preferred choice for large-scale production scenarios such as motor controllers, power battery pack trays, and heat dissipation enclosures. However, in terms of process, impurities, and pores need to be addressed. Sealing rings or friction welding processes are used to ensure reliability and avoid leakage issues.
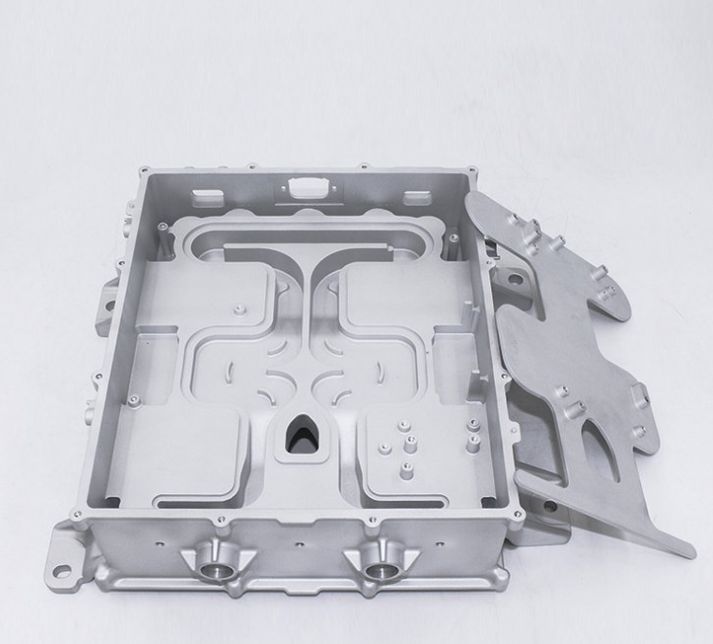
After die-casting, welding is performed. This process is well-controlled, stable, and capable of mass delivery. In addition to friction welding processes, some water-cooling plates may also use brazing or vacuum brazing for welding.