Liquid Cooling System Design, Calculation, and Testing for Energy Storage Solutions
Selection of Energy Storage Solutions
Currently, the most mature and widely used energy storage technologies are pumped storage and electrochemical energy storage. Electrochemical storage primarily utilizes lithium-ion batteries. Considering factors like cost-effectiveness, safety, lifespan, and industry maturity, lithium iron phosphate (LiFePO4) batteries are the most suitable for energy storage today.
For thermal power auxiliary frequency regulation, the energy storage system requires batteries with high discharge rates, rapid response times, high energy efficiency, temperature safety, and long lifespan. Therefore, for combined thermal power and frequency regulation projects, LiFePO4 batteries are recommended. From the user-side storage applications, including peak shaving, demand response, and supply reliability, LiFePO4 batteries are also a recommended choice.
Safety incidents at energy storage stations are frequent. Between 2011 and 2021, there were 32 global fire and explosion incidents at energy storage stations, with 80% involving lithium ternary batteries. In 2021, a fire and explosion at the Beijing Fengtai Energy Storage Station was caused by internal short circuits in the batteries, leading to thermal runaway and fire.
Battery fires are typically caused by thermal runaway, which results from internal short circuits. These can be caused by mechanical, electrical, or thermal abuse. To address thermal abuse, effective thermal management designs are essential.
Liquid Cooling Technology for Energy Storage Systems
Liquid cooling technology uses convective heat transfer through a liquid to dissipate heat generated by the battery and lower its temperature.
The risk of liquid leakage in liquid cooling systems can be minimized through careful structural design. Liquid cooling systems are more efficient than air cooling systems, with better temperature difference control and simpler flow control. They also extend the lifespan of the batteries.
Considering overall costs, liquid cooling systems are superior to air cooling systems. With current safety concerns in energy storage stations, liquid-cooled energy storage systems are being increasingly adopted.
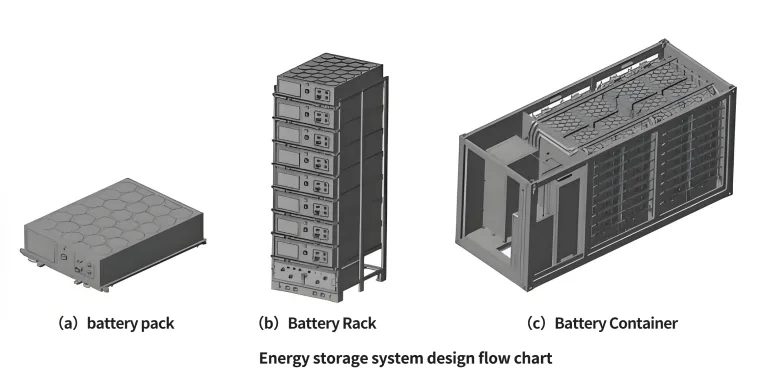
In this study, a liquid-cooled thermal management system is used for an energy storage project. The design of the energy storage system is detailed, offering valuable insights for related designers and engineers.
Liquid-Cooled Lithium Battery Energy Storage System
The lithium battery energy storage system consists of a battery chamber and an electrical chamber. The battery chamber includes the battery pack, liquid cooling system, fire suppression system, combiner box, distribution box, and more. The electrical chamber contains components like the inverter (PCS), transformer, control cabinet, ring network cabinet, AC distribution cabinet, and air conditioning system. This study focuses on the design and development of the battery chamber, while the electrical chamber will be discussed briefly.
The system uses Yiwei Lithium LF280K square aluminum shell LiFePO4 cells (3.2 V/280 Ah). The battery pack is configured in a 1P48S series-parallel arrangement, with 48 cells per pack. The total capacity of each battery pack is 43.008 kWh. The battery system consists of 8 parallel battery racks, each containing 8 battery packs in series, giving the energy storage system a total capacity of 2.75 MWh and a rated voltage of 1,228.8 V. The battery chamber is housed in a standard 20-foot high container (6.058 m × 2.438 m × 2.896 m) with waterproof, thermal insulation, anti-corrosion, fireproof, anti-sand, anti-vibration, and UV protection features. Its protection rating is IP54.
To prevent overcharging and deep discharge of the batteries, a Battery Management System (BMS) is included to manage charge and discharge cycles, ensuring stable and reliable operation. Additional protection hardware, including relays, circuit breakers, and fuses, are also provided.
Thermal Management Design for Energy Storage
Thermal Management System Design
The liquid cooling thermal management system consists of liquid cooling plates, liquid cooling units, piping, high and low-pressure wiring, and coolant. To mitigate leakage risks, several measures are implemented:
- The liquid cooling connectors use automotive-grade leak-proof quick-connect fittings to minimize leakage risks during system operation.
- A liquid level sensor in the expansion tank of the cooling unit detects any leakage and triggers an alarm.
- The battery pack is designed with an IP67 protection rating to prevent any impact on the system in case of leakage. The liquid cooling plate of the battery pack is made from aluminum alloy, integrating the base and cooling plate into a single piece. The cooling plate and sealing cover are joined using friction stir welding, and airtightness tests ensure the sealing performance is up to standard.
The liquid cooling system uses a 50% water and 50% glycol mixture as the coolant, which circulates through the cooling plates to regulate the temperature of the battery pack.
Cooling and Heating Control Strategies
The cooling unit can operate in cooling, heating, and dehumidification modes, depending on the temperature conditions. When the battery’s maximum temperature (Tmax) reaches or exceeds 28°C, the system enters cooling mode. When Tmax is less than 25°C, the system stops cooling. In heating mode, when the minimum temperature (Tmin) is below 12°C, the system activates the PTC heater to warm the batteries. The system switches back to cooling mode when Tmin exceeds 20°C.
In extreme cold conditions (e.g., -30°C), the system preheats the batteries until the temperature reaches 0°C before charging can begin. The liquid cooling unit is custom-designed, and its performance is verified through testing.
Heat Load Calculation and Cooling Requirements
The total heat generated by the battery cells is calculated using the cell’s internal resistance and current. With a total of 3,072 LF280K cells, the total heat generated during a 0.5C charge cycle is 38.4 kW. The cooling capacity of the system is calculated to ensure the liquid cooling system can effectively dissipate this heat, with the cooling unit designed to provide 20 kW of cooling power.
Fire Suppression System
The fire suppression system for the energy storage station uses a gas-liquid two-phase atomized extinguishing agent, along with a combination of aspirating smoke detectors, combustible gas detectors, and temperature/smoke sensors. These detectors monitor the entire energy storage container. In the event of a thermal runaway incident in the battery pack, the system activates the local fire suppression measures, including the release of fire-extinguishing agent and temperature reduction.
The fire suppression system uses FK-5-1-12 (a clean agent) to suppress early-stage fires. In the event of a larger fire, the system automatically switches to a water-based suppression system to provide extended cooling and prevent re-ignition.
Experimental Validation
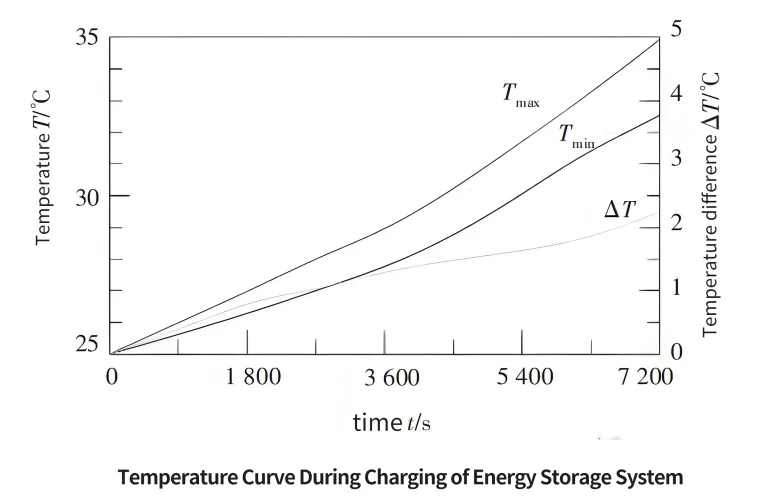
Testing was conducted on the liquid-cooled energy storage container at an ambient temperature of 25°C. During a 0.5C charging test, the surface temperature of the battery cells remained below 35°C, with a temperature rise of less than 10°C. The temperature difference between the cells was less than 2.3°C. This experimental result demonstrates that the liquid-cooled system offers superior thermal consistency compared to air-cooled systems, where temperature differences can range from 5°C to 8°C. This contributes to the longevity and reliability of the entire energy storage system.