What are the different types of capillary structures in heat pipe heat sinks?
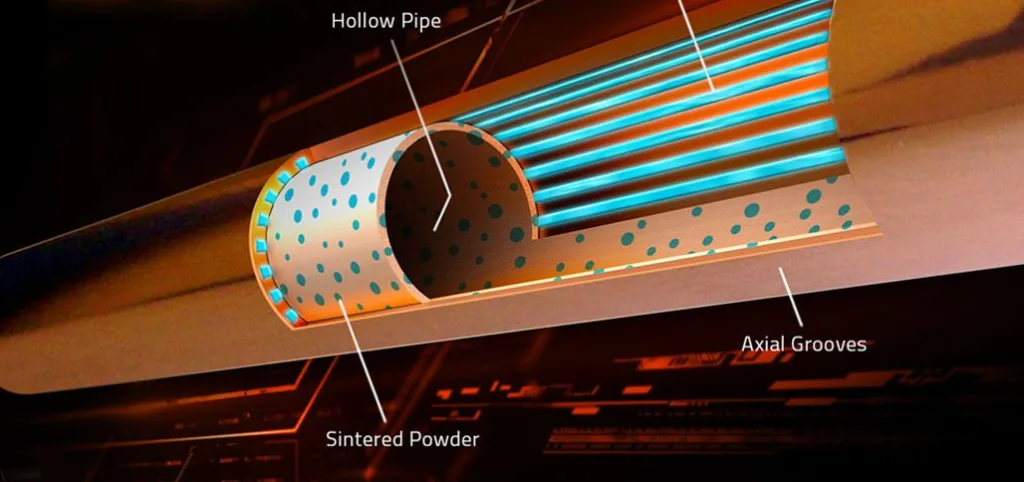
A heat pipe heat sink is a highly effective thermal management solution that utilizes phase change heat transfer. It is composed of a heat pipe cooling module that relies on the working fluid inside to transfer heat efficiently. Heat pipes are commonly used in custom heatsinks to provide optimal cooling performance for electronic devices and machinery. Here are the basic characteristics of heat pipes:
- High thermal conductivity
- Excellent temperature uniformity
- Reversibility of heat flow direction
- Thermal diode and thermal switch behavior
- Environmental adaptability
The thermal switch behavior means a heat pipe can function as a unidirectional heat conductor. For example, when the temperature of segment A is higher than segment B, the heat pipe is active; when the temperature of segment A drops below segment B, the heat pipe ceases to work. This feature is crucial in heat pipe cooling modules used in environments where temperature fluctuations occur.
The heat pipe is particularly effective in applications such as custom heatsinks in electronics, where precise control over heat dissipation is critical. It works by absorbing and transferring heat efficiently through its capillary structure, ensuring the thermal balance required for sensitive components.
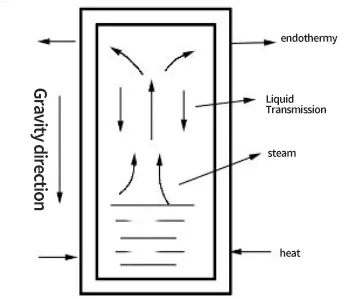
1. Powder Sintered Structure in Heat Pipe Heat Sinks
The powder sintered structure used in heat pipe heat sinks provides a highly efficient capillary action. This method is widely adopted for creating heat pipe cooling modules, especially in custom heatsinks where the need for compact, high-performance cooling solutions is paramount. The sintering process ensures that copper powder, after being heated and cooled, forms a solid and resilient capillary structure capable of supporting the fluid flow in heat pipes.
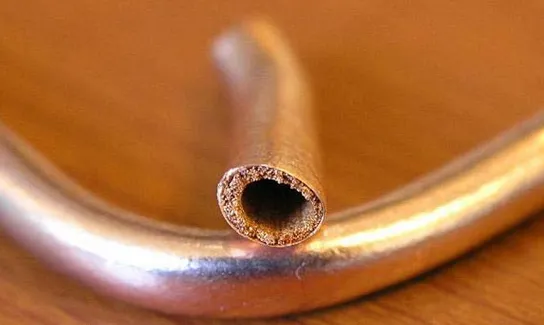
Copper powder sintered capillary core
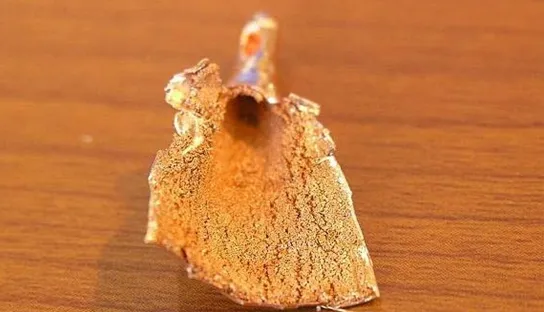
Copper powder sintered capillary core
Copper powder production can be done using three main methods: electrolysis, water atomization, and reduction methods. Electrolytic copper powder tends to have a dendritic microscopic shape with high surface area and purity, though it has high energy consumption and environmental impact. Currently, copper powders produced by the water atomization method are more commonly used. The water atomization + reduction method (AOR) is now the most widely adopted, where the surface of copper powder is modified to develop a non-planar coral-like microstructure with better flow properties and stable performance.
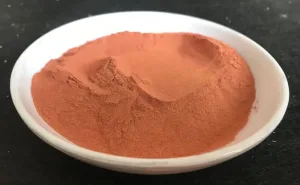
2.Groove Structure in Heat Pipe
The groove structure is another design used in heat pipe heat sinks and heat pipe cooling modules. The grooves act as channels for the working fluid, allowing for effective capillary action. This structure is particularly useful in custom heatsinks where gravity plays a significant role in the fluid return, especially in vertical or oriented applications. While not as efficient as sintered structures, grooves are cost-effective and simple to manufacture.
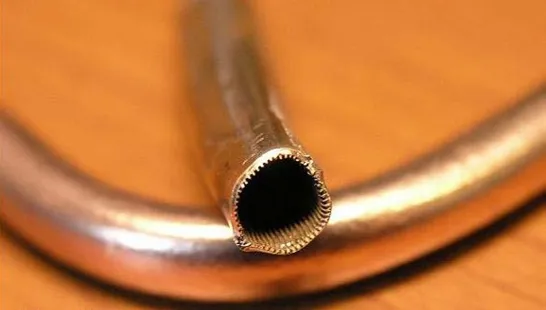
Grooved capillary structure
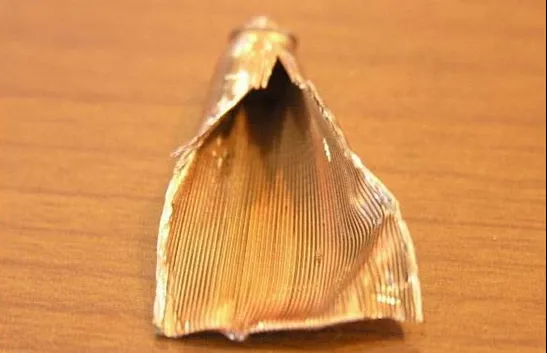
Grooved capillary structure
3.Metal Mesh Structure in Heat Pipe Cooling Modules
The metal mesh structure is a flexible and cost-effective option for heat pipe cooling modules. It is often used in heat pipe heat sinks for applications requiring rapid fluid transport and relatively simple manufacturing processes. While it may not match the performance of sintered powder structures, it still provides a reliable capillary force for many cooling applications.
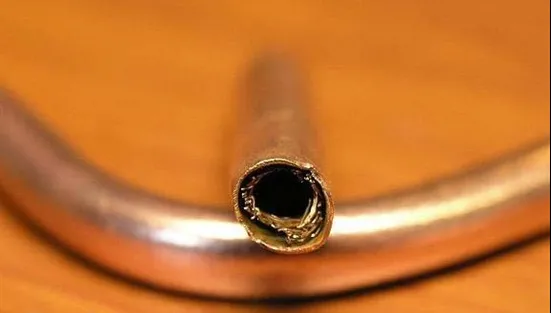
Wire mesh capillary core structure
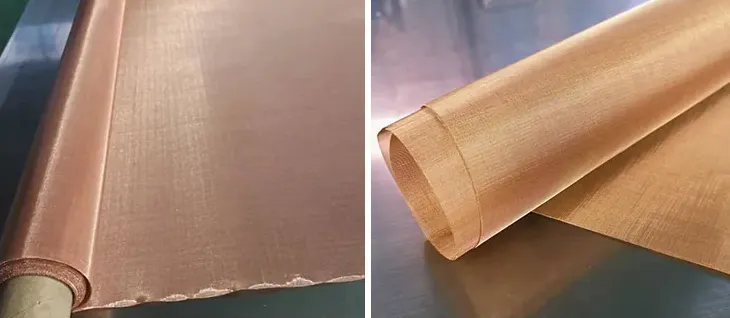
Copper wire mesh
The metal mesh used for capillary structures typically has a mesh number specification, such as 100 mesh, 200 mesh, or 300 mesh.
4. Composite Structure
Given the advantages and disadvantages of the above-mentioned structures, composite heat pipe structures are also widely used today.
For instance, combinations like copper powder + copper mesh or groove + copper mesh are used. For long-distance working fluid transport, metal woven wires can be sintered on the surface of the powder or mesh to improve the return speed and enhance the flow passage.