PCM-Based Heat Sink
As an alternative to forced air/liquid convection cooling and other thermal management methods, PCM (Phase Change Material) cooling is a simple and practical passive thermal management solution that has recently attracted widespread attention in the research community.
The advantages of PCM include: higher latent heat of fusion providing high energy density, controllable temperature stability, and small volume changes during phase transitions.
However, PCM has relatively low thermal conductivity. To enhance the performance of heat sinks, metal fins can be embedded, porous metal structures inserted, heat pipes incorporated, and high-conductivity metal foams and nanoparticles mixed with PCM. These are known as thermal conductivity enhancers.
Proposed the use of fins to improve the thermal conductivity of PCM modules, conducting numerical studies to find the most effective fin configuration that would limit the critical temperature (Ter) of the thermal control module (TCM), as shown in Figure 8. Important fin parameters to consider in the experiment include the size, number, shape, and mass percentage of the fins. The results indicate that the cover plate temperature decreases as the number of fins increases from 9 to 100 per 1/4 geometry, while the increased number of fins enhances local heat diffusion into the PCM, leading to a reduction in the critical temperature value.
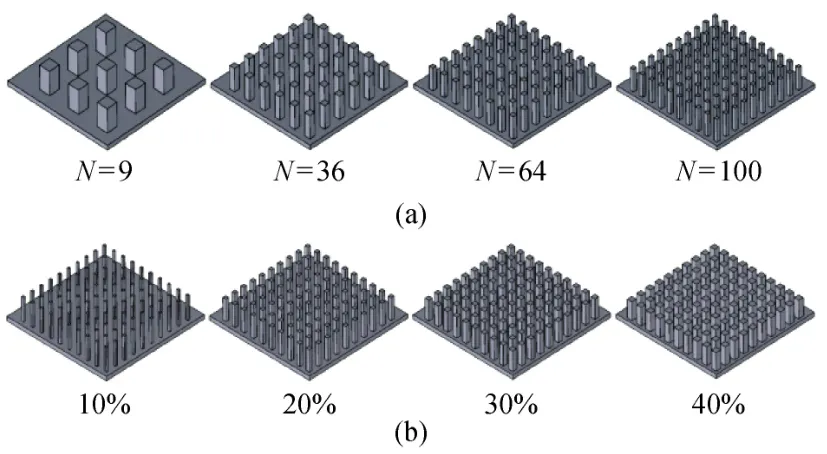
Figure 1: TCM with Different Numbers of Fins and Different Fin Mass Fractions
Experimental studies have shown that embedding different metal structures into PCM-based heat sinks helps enhance the thermal performance of the heat sink. Xie et al. proposed an innovative tree-shaped metal structure, embedded into a PCM-based heat sink, to better spread the heat from the concentrated heat source into the PCM casing, as shown in Figure 2. Numerical simulations were conducted to study the thermal performance of PCM-based heat sinks with different types of embedded metal structures under natural convection conditions, specifically including conventional plate-fin structures and the innovative tree-shaped structures obtained through topology optimization.
Furthermore, conducted further research on the same innovative tree-shaped metal structure. The experiment compared two plate-fin-type PCM casings with metal volume fractions of 20% and 30% as benchmarks, and generated optimized tree-shaped structures with metal volume fractions of 18.7% and 27.6% for comparison. A research method based on the Volume of Fluid (VOF) and enthalpy-porosity methods was established to study the dynamic thermal behavior of the PCM casing.
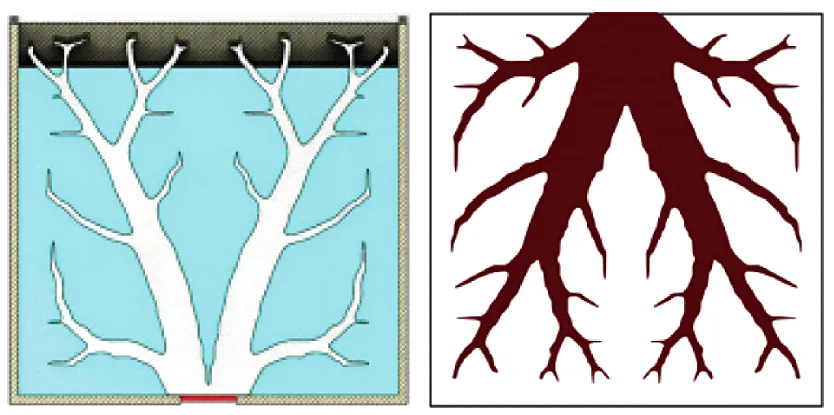
Figure 2: Innovative Tree-Shaped Metal Structure
PCM-based heat sinks mainly utilize the principle of phase change for heat dissipation. In the field of thermal management, PCM can be used for passive cooling or thermal buffering of electronic components that operate intermittently. When PCM melts, it absorbs a large amount of heat, protecting electronic components from overheating. After the component stops working, the heat absorbed by the PCM module is released into the environment, and the PCM solidifies to prepare for the next thermal shock.