Liquid Cooling for Energy Storage——Selection of Cold Plate Technologies for Energy Storage Batteries
This article will provide an in-depth explanation of the selection of cold plate technologies for energy storage batteries.
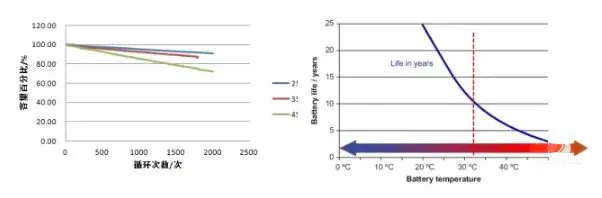
It is not difficult to see from the test data that if a lithium-ion battery exceeds its normal operating temperature, it may experience chemical-level out-of-control. This will not only lead to the decline of the battery’s cycle life and calendar life, but may even cause more serious safety accidents.
How to improve battery performance
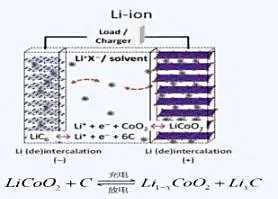
For an energy storage system, it is of utmost importance to always keep the battery cells within an appropriate temperature range. An effective temperature control system can not only ensure the safety and service life of the energy storage power station, but also enhance its performance and efficiency to a certain extent. During this process, we need to focus on solving two problems.
01 Controlling the surface temperature and humidity of a single battery
Maintaining the optimal operating temperature and humidity is the foundation of temperature control. Generally, it is required that the operating temperature of the battery cell is between +15°C and +35°C; the relative humidity is between 5% and 95% and there is no condensed water.
02 Avoiding the generation of local hotspots in the battery system
The temperature difference between the batteries should not exceed 3°C to avoid the generation of local hotspots.
At present, the temperature control mode of the energy storage temperature control system is gradually shifting towards liquid cooling.
Composition of the energy storage liquid cooling temperature control system
The energy storage liquid cooling temperature control system realizes the management of the batteries through steps such as energy storage, energy release, heat dissipation and temperature control, so as to improve the system stability and the battery life.
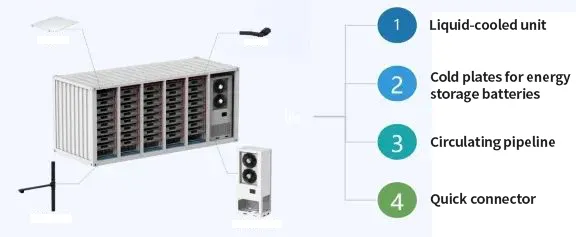
Energy Storage Isothermal Liquid Cooling Plate
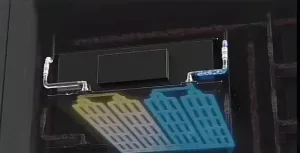
The isothermal liquid cooling plate for energy storage batteries is a heat dissipation technology applied to energy storage batteries. It can effectively control the temperature of the batteries, improving their service life and safety. The liquid cooling plate can absorb the heat generated by the batteries through the circulation of the liquid, thus reducing the temperature of the batteries.
Working principle of the liquid cooling plate
The principle of the isothermal liquid cooling plate is to use a non-conductive liquid as the cooling medium to achieve uniform heat dissipation within the battery pack. The sensor detects the temperature of the battery pack, and the temperature control system adjusts the temperature of the coolant to ensure that the temperature of the battery pack remains uniform. The liquid cooling circulation system of the isothermal liquid cooling plate can effectively reduce the temperature rise of the battery pack, prevent the generation of hot spots, reduce the temperature gradient, and extend the service life of the battery.
Selection of cold plate technologies for energy storage batteries.
Stamped and brazed thin plates
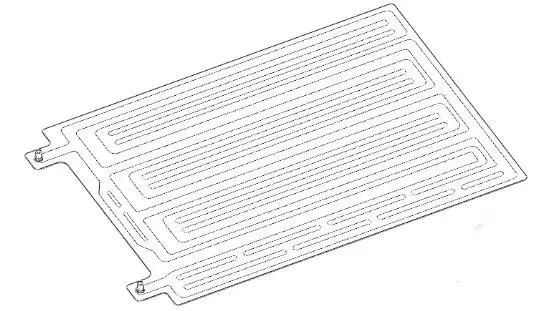
Scenario: Containerized energy storage batteries Operating conditions: 0.5C; 1C Cooling mode: Bottom liquid cooling
Stamped and brazed bottom plate
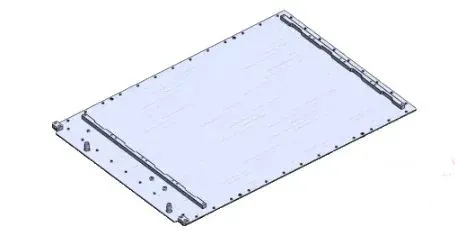
Scenario: Container energy storage batteries Operating conditions: 0.5C; 1C Cooling method: Bottom liquid cooling
Aluminum extruded profile lower box body
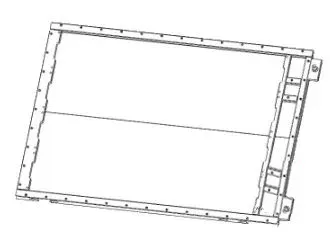
Scenario: Containerized energy storage batteries Operating condition: 0.5C Cooling form: Bottom liquid cooling
It can be seen that the current mainstream technical directions of liquid cooling plates are brazing and profiles. Then, are there any differences between these two different technologies in practical applications? And how should we make a choice between them in actual use?
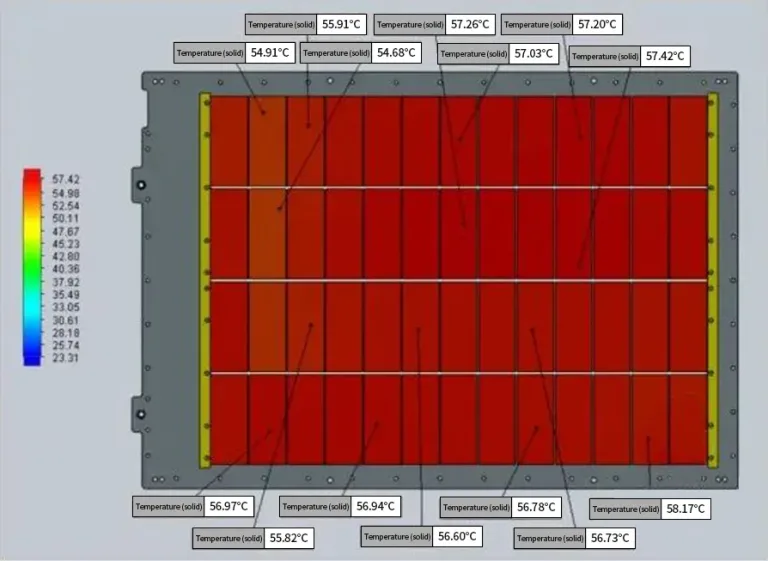
Under the test conditions of a battery thermal power of 1716W@1C, a water flow rate of 10L/min, an inlet water temperature of 18°C, and a coolant of 50% ethylene glycol aqueous solution. The temperature differences between the brazed cold plate and the profile cold plate are as follows:
Type | Maximum Temperature | Temperature Difference of Batteries |
---|---|---|
Brazed Cold Plate | 57.42℃ | 2.74℃ |
Profile Cold Plate | 60.01℃ | 5.86℃ |
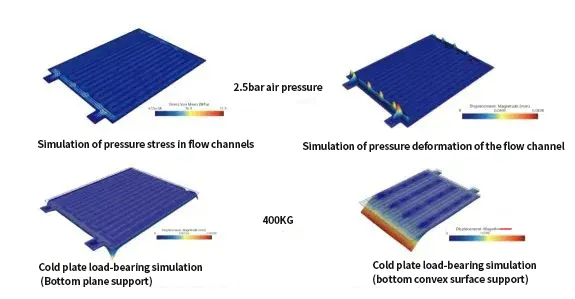
Mechanical Simulation of Battery Cold Plate
Liquid cooling solution for high-rate charging and discharging.
Simulation conditions:
The battery thermal power is 2176W@1C, the water flow rate is 15L/min, the inlet water temperature is 18°C, and the coolant is a 50% ethylene glycol aqueous solution.
Bottom cooling solution
The bottom cooling solution has addressed the temperature differences among different batteries in the battery pack. Nevertheless, owing to the low thermal conductivity of the batteries themselves, the temperature difference between the top and the bottom of the batteries is excessively high, reaching up to 35°C.
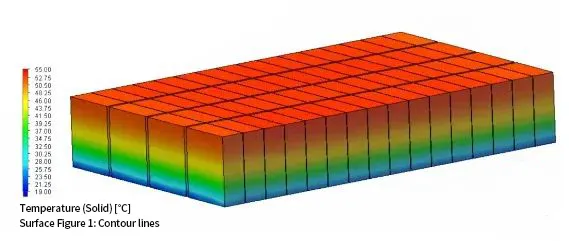
Side cooling solution
The side cooling solution can not only solve the temperature differences among different batteries in the battery pack, but also address the problem of the excessively high temperature difference between the top and the bottom of the batteries.
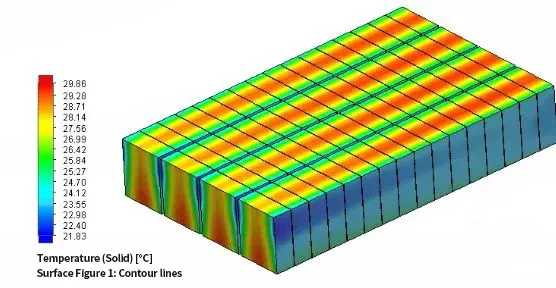