Design of Heat Pipe Heat Sinks for Electronic Devices
Heat Pipes
Heat pipes are fundamental and widely used thermal conductive components in thermal management systems and products. They offer numerous advantages: broad application scenarios, diverse bending and forming options, strong heat dissipation capability, low cost, stable and reliable performance, and long service life. However, as phase-change products, heat pipes also have certain operational limits.
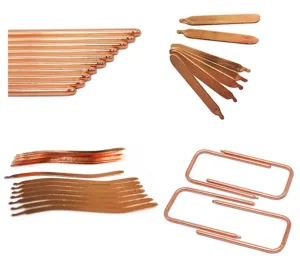
Basic Knowledge/Introduction to Heat Pipes
A heat pipe is a heat transfer element with extremely high thermal conductivity, invented in 1964 at the Los Alamos National Laboratory in the United States. It began widespread industrial use in the 1970s. By leveraging the vapor-liquid phase change of a working fluid within a fully sealed vacuum tube, heat pipes achieve thermal conductivity hundreds of times higher than pure copper, earning them the title of “thermal superconductors.” Well-designed heat pipe CPU coolers deliver performance far superior to traditional fan-cooled heatsinks without heat pipes.
Traditional heatsinks rely on refrigerants, water, or air as working fluids, requiring pumps or fans for circulation. These systems consume significant power, suffer from impurity-induced wear, and incur high maintenance costs. In contrast, heat pipe heatsinks excel in compact structure, high heat transfer capacity, easy installation, and minimal maintenance.
1. Working Principle of Heat Pipe Heatsinks
Heat pipe technology differs from conventional heatsinks by utilizing the evaporation and condensation of a working fluid to transfer heat. A heat pipe consists of three parts: a tube shell, a capillary wick, and a working fluid. The tube is evacuated to a high vacuum, filled with the working fluid to saturate the capillary wick, and then sealed.
A heat pipe has two ends: the evaporation end (heated end) and the condensation end (cooling end), separated by insulation. When one end is heated (creating a temperature gradient), the liquid in the capillary wick evaporates. The vapor flows to the cooler end under pressure differences, releases heat, condenses back into liquid, and returns to the evaporation end via capillary action.
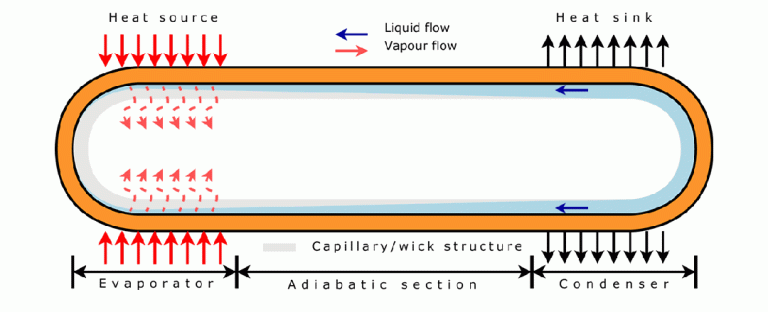
2. Classification and Features of Heat Pipe Heatsinks
Based on operating temperature, heat pipes are categorized as:
Cryogenic heat pipes: Operating range (100–200 K), using helium, argon, nitrogen, or oxygen.
Low-temperature heat pipes: Operating range (200–550 K), using water, Freon, ammonia, alcohol, or acetone.
Medium-temperature heat pipes: Operating range (550–750 K), using Dowtherm A, mercury, sulfur, or cesium.
High-temperature heat pipes: Operating range (>750 K), using potassium, lithium, aluminum, or silver.
Features of Heat Pipe Heatsinks:
High heat transfer efficiency via phase change.
Uniform temperature distribution due to saturated vapor.
Adjustable heat flux density.
Excellent temperature stability.
3. Design of Heat Pipe Heatsinks for Electronic Devices
3.1 Design Requirements for Heat Pipes
Operating temperature: Typically -50°C to 200°C, based on device thermal control needs.
Heat load: Determined by device power and environmental conditions.
Thermal characteristics: Design evaporation/condensation ends, wick, and shell geometry according to power and temperature control requirements (uniformity, stability).
Environment: Account for gravity effects (terrestrial, marine, or aerospace) and cooling medium interfaces.
Dimensions/weight: Meet user specifications for size and weight.
3.2 Working Fluid Selection
Criteria:
Operating temperature between freezing and critical points, preferably near boiling point.
Non-toxic, non-flammable, safe.
Compatible with shell/wick materials.
High figure of merit; capillary lift under gravity.
Common fluids for electronics: Methane, ammonia, Freon, acetone, methanol, ethanol, heptane, water, Dowtherm A.
3.3 Wick Selection
The wick structure and performance are critical. Types include uniform or composite wicks. Key requirements:
Effective capillary pumping to overcome viscous pressure drops.
Sufficient fluid lift height to counteract gravity.
Balance between large pores (minimizing losses) and small pores (maximizing capillary force).
Additional considerations:
Compatibility with fluid and shell.
High permeability and heat transfer.
Rigidity for tight contact with shell.
Ease of manufacturing, reliability, and cost-effectiveness.
3.4 Shell Design
Materials: Copper, oxygen-free copper, aluminum alloy, or stainless steel. Must be compatible with the working fluid, wettable, highly conductive, and mechanically robust.
Structure:
Wall thickness: Balance thermal transfer (thin) and strength (thick). Optimize for minimal thickness while ensuring safety.
Surface: Smooth or finned (aligned with heatsink requirements).
Shape: Typically cylindrical with welded flat-end caps (using TIG or hydrogen-protected welding).
Extension: Sleeve connection method, where two heat pipes are joined via an intermediate sleeve. Contact quality and area determine heat transfer efficiency.
4. Conclusion
Designing heat pipe heatsinks for electronic devices involves selecting appropriate working fluids, wicks, and shells based on specifications, verifying heat transfer performance, and validating through testing. This ensures a robust, efficient, and reliable thermal solution.
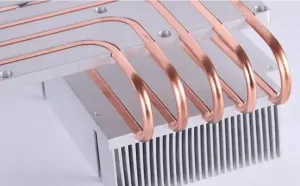