Active Cooling and Air Cooling Technology
Active Cooling
The heat dissipation methods of heat sinks are divided into active cooling and passive cooling.
Passive cooling refers to the process of heat dissipation through the convection and radiation of heat between the fins and the air, without the assistance of external forces.
Active cooling, on the other hand, involves adding external forces to this process, such as fans, liquid cooling, etc., to enhance heat dissipation.
This can effectively improve the heat dissipation efficiency of the heat sink by 1 to 2 energy levels. Active cooling is generally divided into two forms: air cooling and liquid cooling technologies.
Air Cooling Technology
With the high integration and large power of IGBT power devices, heat dissipation issues have become increasingly prominent.
The cooling requirements for IGBT power semiconductor modules are also getting higher.
It is difficult to provide adequate cooling for high-power and high-heat flux IGBT modules with air cooling. Natural convection cooling technology can no longer meet the heat dissipation needs of IGBT power devices, which necessitates the use of forced air cooling technology to accelerate the cooling of IGBT modules and lower their temperature.
Measures to enhance air cooling primarily include increasing the heat dissipation area, improving the heat transfer coefficient, and designing the airflow path reasonably.
Analyzed and studied gas-based cold plates, establishing a mathematical model for the uneven distribution of heat sources on the surface of the cold plate, as shown in Figure 1. The heat transfer path is: baseplate → cold plate channel → gas fluid. Zhao Lianquan and others conducted experimental analysis and research on the transient heat transfer characteristics of high-temperature steel plates in air jet cooling, as shown in Figure 2. The results showed that the heat transfer coefficient is influenced by temperature changes on the impacted surface during the process, and increasing the gas flow rate can improve the heat transfer capability.
others explored the heat dissipation performance of foam aluminum fins in IGBT power semiconductor modules. The results showed that, unlike ordinary fin heat sinks, foam aluminum fin heat sinks can enhance the heat transfer of IGBT power devices and reduce the temperature of power devices due to their larger surface area and irregular internal channels, thus improving the performance and reliability of power electronic devices.
Compared to natural cooling, forced air cooling can increase the heat dissipation by 5 to 12 times. However, forced air cooling has the issue of requiring fans and airflow paths, and its reliability and cooling efficiency are still relatively low, often generating significant noise.
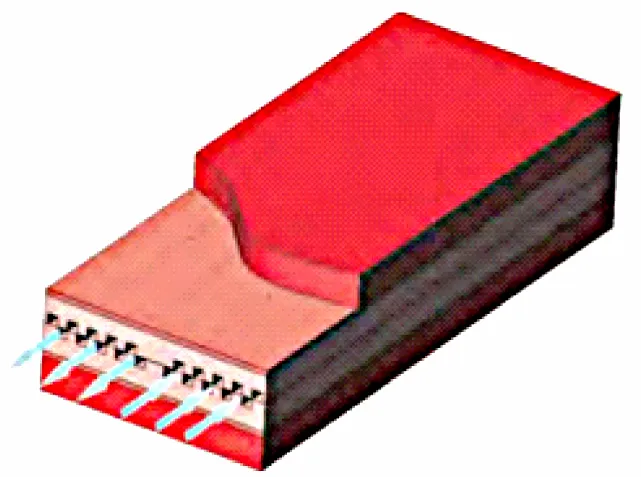
Figure 1 Gas Flow in Cold Plate
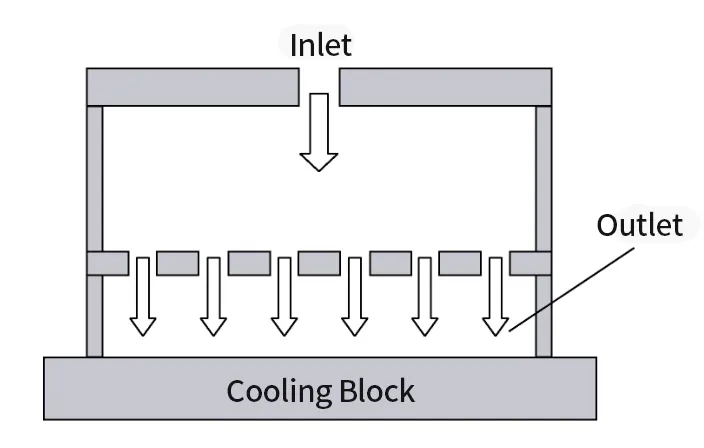