Aluminum Heat Sink Guide: Materials, Design, and Extrusion Types Explained
Discover everything about aluminum heat sinks, from materials and extrusion types to design tips and comparisons with copper. Learn how to choose the best aluminum heat sink for your needs.
1. Aluminum Heat Sink Basics: What Is It and Why It Matters
• What Is an Aluminum Heat Sink and How Does It Work?
An aluminum heat sink is a passive thermal management component designed to dissipate heat from electronic devices and mechanical systems. Made from thermally conductive aluminum heat sink material, it absorbs and disperses heat away from high-temperature components such as CPUs, LEDs, or power transistors.
Heat sinks work by increasing the surface area in contact with air, allowing for efficient heat transfer through convection. Aluminum heat sinks are especially popular due to their excellent thermal conductivity-to-weight ratio and cost-effectiveness.
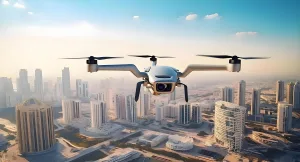
• Key Advantages of Using Aluminum Heat Sinks in Electronics
Using aluminum heat sinks in electronics offers multiple advantages. First, aluminum is lightweight yet provides good thermal conductivity, making it ideal for compact electronic devices. Second, extruded aluminum heat sinks are easy to manufacture into custom shapes, allowing for design flexibility. Additionally, aluminum resists corrosion, prolonging the lifespan of the device.
Compared to copper, aluminum heat sinks are more economical and easier to integrate into high-volume manufacturing lines, particularly in the LED lighting and computer industries.
• Common Applications of Aluminum Heat Sink Blocks and Enclosures
Aluminum heat sink blocks and aluminum heat sink enclosures are widely used across industrial and consumer electronics. In power supplies and inverters, solid aluminum blocks ensure stable thermal control. Meanwhile, aluminum heat sink enclosures are integrated directly into device housings to function both as protective casings and heat dissipation units.
Applications range from automotive electronics and 5G base stations to LED drivers and network routers.
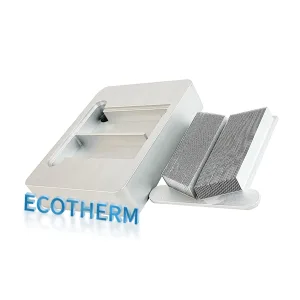
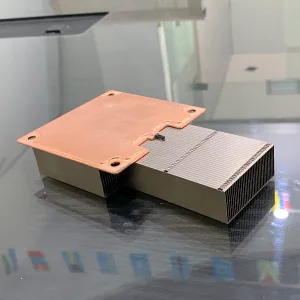
• The Role of Aluminum Heat Sink Fins in Thermal Management
Aluminum heat sink fins dramatically improve cooling efficiency by increasing the surface area exposed to air. These finned aluminum heat sinks promote natural or forced convection, enabling faster heat dissipation.
Designs such as aluminum fin heat sinks or round aluminum heat sinks are tailored for different airflow dynamics. The fin geometry—spacing, height, and thickness—plays a crucial role in maintaining optimal device temperatures and preventing thermal overload.
2. Aluminum Heat Sink vs Copper Heat Sink: A Practical Comparison
• Thermal Conductivity: Comparing Copper vs Aluminum Heat Sink Efficiency
When it comes to thermal conductivity, copper heat sinks outperform aluminum. Copper has a conductivity of ~400 W/m·K compared to aluminum’s ~235 W/m·K. However, copper vs aluminum heat sink performance also depends on application design.
In high-power or compact environments, copper may be preferred. But in systems with larger surface areas or airflow optimization, a well-designed aluminum heat sink—especially one with efficient fins—can offer competitive thermal performance at a fraction of the cost and weight.
• Weight and Cost Factors: Why Aluminum Heat Sinks Are Widely Used
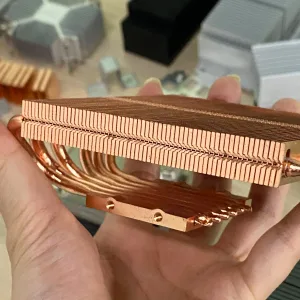
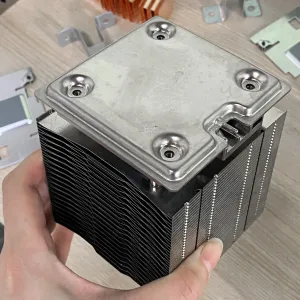
Aluminum heat sinks are significantly lighter than copper—about one-third the weight—which makes them ideal for mobile devices, drones, or automotive electronics.
Additionally, aluminum heat sink material is far more cost-effective and easier to source in bulk. These weight and cost advantages explain why extruded aluminum heat sinks dominate industries like LED lighting, consumer electronics, and telecommunications.
• Manufacturing Process: Extruded Aluminum Heat Sink vs Machined Copper
The manufacturing process greatly influences material choice. Extruded aluminum heat sinks can be mass-produced in complex shapes quickly and economically. In contrast, machined copper heat sinks require longer processing times and more expensive tooling.
The aluminum extrusion heat sink process allows for integrated fins, optimized airflow paths, and enclosure-ready formats—perfect for scalable production.
• Which One to Choose? Application-Based Recommendations
For most general-purpose applications like computers, power supplies, and LED fixtures, an aluminum heat sink provides the best balance of thermal performance, cost, and manufacturability.
However, for high-frequency or ultra-high-power applications—such as RF amplifiers or industrial lasers—a copper heat sink may be justified due to superior thermal performance.
Ultimately, the decision between aluminum vs copper heat sink depends on your project’s size, weight constraints, thermal load, and budget.
3. Extruded Aluminum Heat Sink Types: From Fins to Blocks
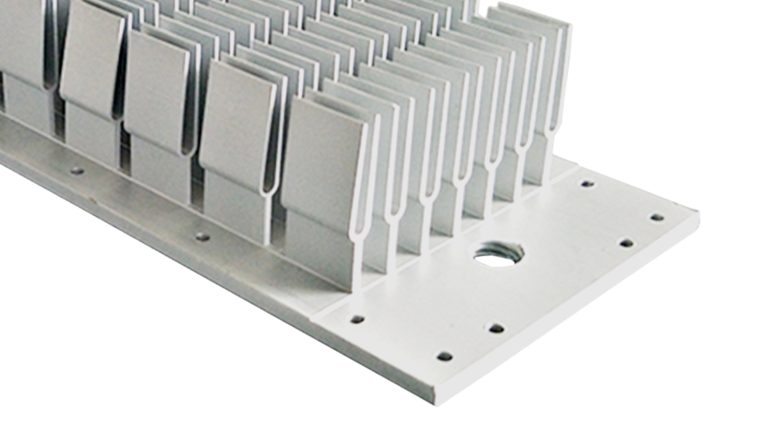
• What Is an Extruded Aluminum Heat Sink?
An extruded aluminum heat sink is a thermal management component produced by forcing molten aluminum through a die to create a fixed cross-sectional profile. This aluminum extrusion heat sink process enables manufacturers to form complex shapes—such as integrated fins or slots—at scale, with high dimensional accuracy.
Extruded aluminum heat sinks are favored in electronics, LED systems, and power modules due to their lightweight structure, customizable geometry, and excellent surface area-to-weight ratio.
• finned aluminum heat sink, round aluminum heat sink
A finned aluminum heat sink features multiple narrow fins extending from the base, significantly increasing surface area for convective heat transfer. These designs are commonly used in passive cooling systems where natural or forced airflow is available.
Whether it’s a linear, straight-fin structure or a pin-fin variant, aluminum heat sink fins help regulate temperature efficiently in applications like lighting, industrial controllers, and inverters.
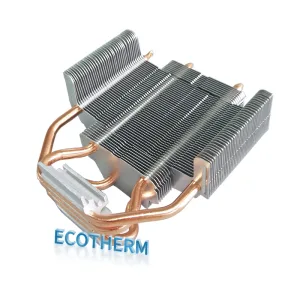
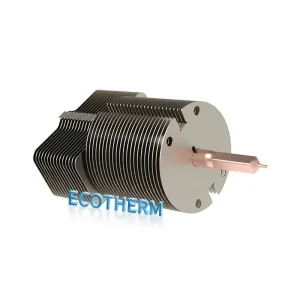
4. Aluminum Heat Sink Material: What Makes It Ideal for Cooling?
• Common Aluminum Alloys Used in Heat Sink Manufacturing
Aluminum heat sink material is typically made from alloys such as 6061 and 6063, which offer a strong balance of thermal conductivity, workability, and corrosion resistance.
6063 aluminum, in particular, is favored for extruded aluminum heat sink production due to its smooth surface finish and excellent ability to form thin, complex fins. These alloys ensure reliable performance in electronic, automotive, and lighting systems.
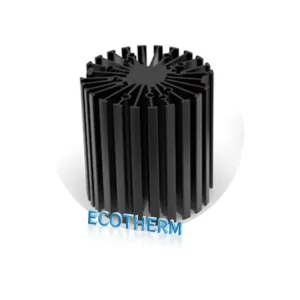
• Benefits of Extruded Aluminum Heat Sink Material for Heat Transfer
The extruded aluminum heat sink material provides outstanding benefits for thermal management. The extrusion process allows for uniform density and optimal heat flow along the length of the sink.
Thanks to aluminum’s natural thermal properties, extruded aluminum heat sinks can effectively dissipate heat across large surface areas while maintaining structural integrity and manufacturing efficiency.
• Aluminum Heat Sink Plate and Surface Treatments
An aluminum heat sink plate serves as a flat, thermally conductive base for mounting heat-generating components. These plates are often anodized or chemically treated to improve corrosion resistance and thermal radiation.
Surface treatments also enhance bonding with thermal interface materials (TIMs), allowing aluminum heat sink plates to maintain consistent performance in demanding conditions.
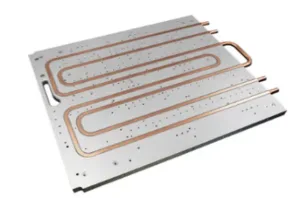
• Lightweight and Corrosion Resistance: Core Strengths of Aluminum
A key reason why aluminum heat sink material is so widely used lies in its lightweight nature and excellent corrosion resistance. These properties make aluminum ideal for mobile devices, aerospace systems, and outdoor electronics, where weight reduction and durability are critical.
Unlike heavier metals, aluminum heat sinks offer ease of installation without compromising cooling capacity, contributing to both design efficiency and long-term reliability.
5. Aluminum Heat Sink Design: Key Principles and Tips
• Aluminum Heat Sink Design Basics: Airflow, Surface Area, and Thermal Path
Effective aluminum heat sink design begins with three core elements: optimized airflow, sufficient surface area, and a direct thermal path.
Maximizing surface exposure to moving air enhances heat dissipation, while minimizing the distance from the heat source to the sink surface improves thermal transfer. A well-designed aluminum extrusion heat sink balances these elements for efficient passive or active cooling performance.
• How to Optimize Aluminum Heat Sink Fins for Maximum Cooling
Proper aluminum heat sink fins are crucial for maximizing convective heat transfer. Fin spacing, height, and thickness must align with airflow type—natural or forced.
Wide fin spacing benefits passive systems by reducing thermal resistance, while dense, narrow fins suit high-speed fan environments. Advanced finned aluminum heat sink designs can include pin-fin or serrated profiles to improve turbulence and cooling efficiency without increasing weight.
• The Role of Aluminum Heat Sink Plate Thickness and Geometry
The aluminum heat sink plate serves as the thermal base, conducting heat from the component to the fins. Plate thickness and geometry directly affect temperature spread and overall efficiency.
A thicker aluminum heat sink plate helps manage high heat loads but increases weight. Geometries like spreaders or cutouts can enhance compatibility with PCB layouts or enclosures, enabling tighter system integration and more effective cooling.
• Surface Finishing in Aluminum Heat Sink Design: Anodizing & Coating
In aluminum heat sink design, surface treatment is more than aesthetics. Anodizing improves corrosion resistance and enhances emissivity, aiding thermal radiation in passive systems.
Black anodized aluminum heat sinks are especially effective in natural convection environments. Additional coatings such as chromate or powder coating may be used for environmental protection or branding, without compromising thermal performance.
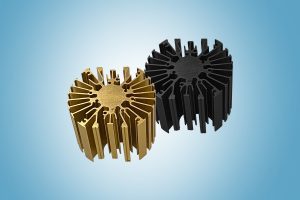
6. Aluminum Heat Sink Manufacturers: How to Choose a Reliable Partner
• What to Look for in Aluminum Heat Sink Manufacturers
When selecting aluminum heat sink manufacturers, it’s not just about finding the lowest price — it’s about finding a team that truly understands your thermal requirements. A reliable aluminum heat sink manufacturer should have in-house capabilities for aluminum extrusion, CNC machining, and anodizing, along with a proven track record in industries like LED lighting, power electronics, automation, and telecommunications.
Look for manufacturers who offer full design support, respond quickly to engineering changes, and can scale production from prototype to mass production without sacrificing quality.
• Custom Aluminum Extrusion Heat Sink Services and Capabilities
If you need a solution tailored to your specific application, custom aluminum extrusion heat sink services are essential. A professional supplier should offer flexibility in fin geometry, surface treatments, mounting features, and block dimensions.
Whether it’s a high-density finned aluminum heat sink, a round aluminum heat sink for LED modules, or a large aluminum heat sink block for industrial power supplies, the ability to customize efficiently will directly impact your product’s thermal performance and overall success.
• Evaluating Aluminum Heat Sink Quality: Material, Tolerances, and Certifications
Evaluating aluminum heat sink quality comes down to a few key factors:
Material: Ensure the use of high-grade 6061 or 6063 aluminum heat sink material with excellent thermal conductivity and strength.
Tolerances: Tight machining tolerances ensure a proper fit, better heat transfer, and easier integration into your system.
Certifications: Look for manufacturers that meet ISO 9001, RoHS, and industry-specific standards to ensure consistent quality and environmental compliance.
These standards are not just about quality — they’re a sign that your manufacturing partner is serious about long-term reliability.
Looking for a Trusted Custom Aluminum Heat Sink Manufacturer?
If you’re looking for a reliable partner to solve high-power thermal challenges, we’re here to help. We specialize in custom aluminum heat sinks, with over 20 years of experience focused exclusively on thermal solutions for high-power applications.
At our factory, we don’t just manufacture — we collaborate with you every step of the way. Whether you have an early-stage concept or a complex thermal problem, we offer:
Free drawing analysis to assess manufacturability and performance
Free thermal simulation to optimize your heat sink design
Free custom design or redesign support, including testing and validation
Full in-house capabilities including aluminum extrusion, CNC machining, and surface finishing
Proven success in industries like power electronics, EV, industrial automation, energy storage, and more
We’re not a catalog company — we’re a team of experts dedicated to building custom cooling solutions that actually work in the field.
📩 Contact us today to discuss your project. Let’s engineer a better way to dissipate heat — together.
7. Aluminum Heat Sink HS Code: Understanding Import/Export Requirements
• What Is an Aluminum Heat Sink HS Code
The aluminum heat sink HS code is like an international ID number for aluminum heat sinks when they’re shipped across borders. It helps customs officers quickly identify what the product is, so your shipments can clear smoothly and without unnecessary delays.
Usually, extruded aluminum heat sinks fall under HS codes like 76042990, which covers aluminum profiles and extrusions. But the exact code can change a bit depending on whether your aluminum heat sink is raw, machined, anodized, or combined with other parts like LED modules or fans.
Knowing the right HS code for aluminum heat sink blocks, fins, or enclosures means you can avoid surprises at customs, pay the right tariffs, and have all the paperwork in order.
If you’re new to importing or exporting aluminum heat sinks, don’t worry! Your supplier or freight forwarder can help figure out the correct code. And if you work with an experienced aluminum heat sink manufacturer, they’ll gladly assist you with this too.
8. How to Choose the Right Aluminum Heat Sink for Your Project
Choosing the right aluminum heat sink is essential for ensuring efficient thermal management and long-term reliability in your project. Several key factors influence the selection of the perfect aluminum heat sink, from project requirements to material and design considerations.
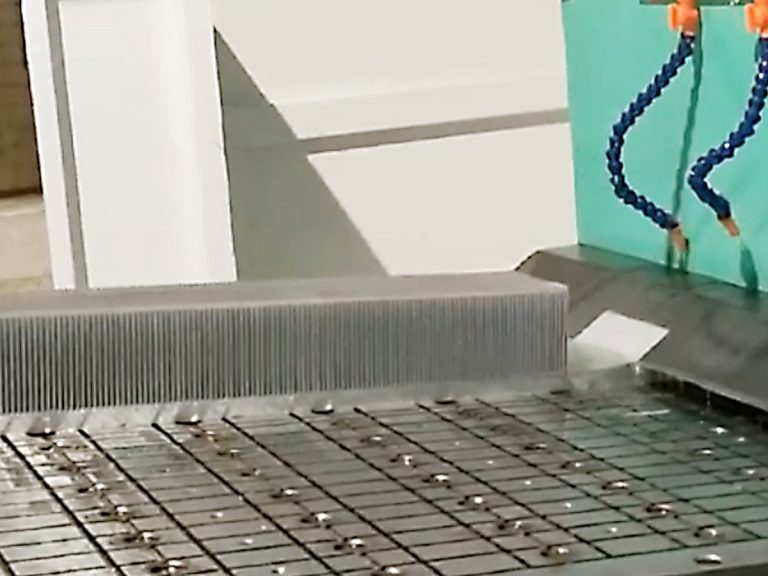
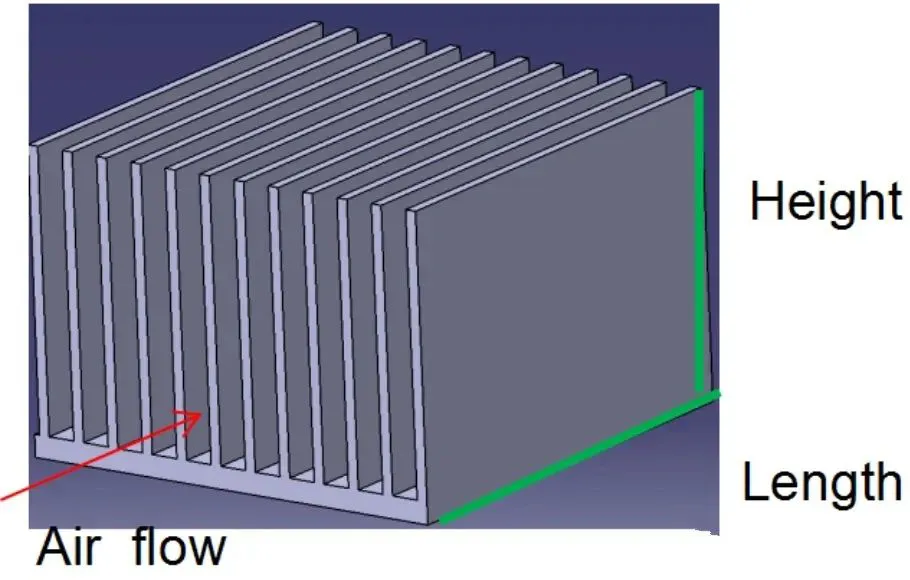
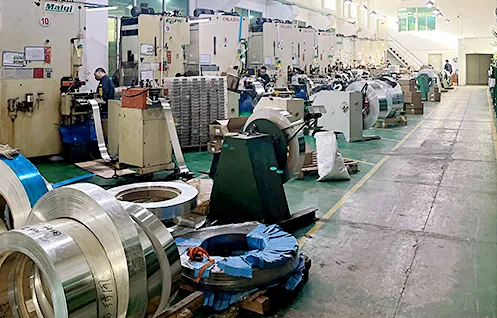
• Project Requirements That Affect Aluminum Heat Sink Selection
Before selecting an aluminum heat sink, clearly define your project’s thermal needs. Consider the power dissipation, operating environment, size constraints, and airflow conditions. For example, high-power electronics often need larger finned aluminum heat sinks with optimized fin spacing to maximize heat dissipation. Compact devices might benefit from extruded aluminum heat sink designs that balance size and performance.
•Choosing Between Extruded, Finned, and Block Aluminum Heat Sinks
The choice between extruded aluminum heat sinks, finned aluminum heat sinks, and aluminum heat sink blocks depends largely on your application and manufacturing needs.
Extruded aluminum heat sinks offer customizable fin patterns and cost-effective production for medium to large volumes.
Finned aluminum heat sinks provide superior surface area for airflow, ideal for cooling CPUs, LEDs, and power modules.
Aluminum heat sink blocks are solid, often used in high-power applications requiring direct contact and uniform heat spread.
• Aluminum vs Copper Heat Sink: Which Fits Your Application?
When deciding between aluminum vs copper heat sinks, weigh factors like thermal conductivity, weight, cost, and corrosion resistance. While copper has higher thermal conductivity, aluminum heat sinks are lighter, more affordable, and easier to manufacture—making them suitable for most electronics cooling needs. For applications where weight or cost is critical, aluminum is usually the preferred choice.