Custom
Skived Heat Sink Products
Tailored Solutions for High-Power Applications
Up To 3000mm Length
Free Thermal Analysis
Double-side Skived Fin
Wavy Skived Fin
Custom Manufacturing of Skived Heat Sinks up to
3 Meters Long and 90cm Wide
What is Skived heat sinks
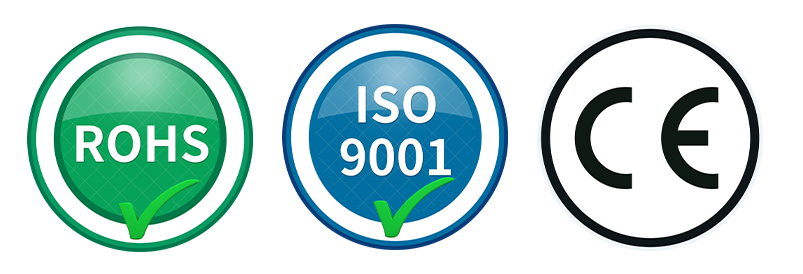
Skived heat sinks are made by precision skiving of metal profiles, usually copper or aluminum, at specific angles and intervals to create high-density fins perpendicular to the base. This process results in thinner, denser fins, significantly increasing the surface area for improved heat dissipation.
These heat sinks are typically made from copper or aluminum, known for their excellent thermal conductivity—copper at 401 W/m·K and aluminum at 237 W/m·K. The skiving method minimizes thermal resistance when compared to conventional welding or pin-fin structures, improving heat dissipation. Furthermore, supplementary post-processing methods, such as incorporating copper tubes or utilizing surface treatments, can enhance cooling effectiveness even more.
Skived heat sinks are often considered a type of heat sink that can be customized to meet specific requirements, but they also come in standard versions suitable for various applications.Thanks to their superior thermal conductivity, compact design, and durability, skived heat sinks are ideal for a wide range of high-efficiency cooling applications. Custom heat sinks can be designed to fit unique configurations, ensuring optimal cooling performance in specialized devices. With increasing market demand, new designs such as wave-shaped and double-sided skived heat sinks are also available, offering even greater flexibility and cooling power.
Explore Our Range of Tailored High-Power Designs
Skived Heat Sinks Case Product Display
Wave Heat Sink with Fins for Hole Clearance
Double-sides Skived Heat Sink
Skived Heat Sink with Heat Pipe, Hole for CNC
Copper & Aluminum ,Different Size Heat Sink
Customize your own heat sink?
1.Advantages of skived heat sink
- Integrated Molding: No gaps or thermal resistance between the fins and the baseplate.
- Minimal Mold Cost: Significantly reduced mold manufacturing cost.
- Fast Delivery Capability: Quick turnaround times for orders.
- Maximum Dimensions: Can be produced up to 3m in length and 900cm in width.
- Ultra-thin Fins and Density Control: Aspect ratio can reach up to 50:1.
- Customizable Options: Customizations available, such as heat pipe integration.
- Maximum Heat Dissipation with Forced Convection: Enhanced thermal performance under forced air cooling.
- Improved Natural Convection Performance: Optimized for better heat dissipation via natural convection.
2.Material properties accurate selection
Model
Thermal Conductivity (W/m·K)
Applications
C11000 Pure Copper
390-400
5G base stations, servers (cost-sensitive)
C10100 Oxygen-Free Copper
390-400
Aerospace electronics, vacuum environments
1060/1070 Pure Aluminum
230-240
Consumer electronics, LED lighting
6063 Aluminum Alloy
200-210
Automotive equipment, industrial frequency converters
Model | Thermal Conductivity (W/m·K) | Applications |
---|---|---|
C11000 Pure Copper | 390-400 | 5G base stations, servers (cost-sensitive) |
C10100 Oxygen-Free Copper | 390-400 | Aerospace electronics, vacuum environments |
1060/1070 Pure Aluminum | 230-240 | Consumer electronics, LED lighting |
6063 Aluminum Alloy | 200-210 | Automotive equipment, industrial frequency converters |
3.Surface Treatment Specifications
Copper Heat Sink
Treatment Type
Anti-oxidation
Nickel Plating
Aluminum Heat Sink
Treatment Type
Transparent Anodized
Black Anodized
Chemical Conversion Coating
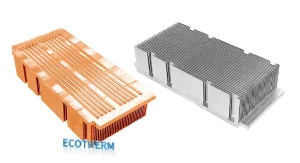
4.Maximum Size Limits
Ecotherm can produce skived heat sinks with a maximum size of 3meter and a width of 900cm
Material | Fin Thickness | Width | Length | Fin Heigh | Fin Pitch |
---|---|---|---|---|---|
Copper | 0.1-1mm | ≤900mm | ≤3000mm | ≤80mm | 0.16-12mm |
Aluminum | 0.2-2mm | ≤900mm | ≤3000mm | ≤130mm | 0.2-12mm |
5.Fin Structure Design Guidelines
Thickness-Height Relationship
- Copper Fins: 0.1mm thick → 15mm high (straight) / 18mm (curved)
- Aluminum Fins: 0.2mm thick → 25mm high (straight) / 30mm (curved)
Edge Safety Distance
- Distance from the first and last fins to the substrate edge ≥ 50% of the fin spacing
- Tolerance of ±1 fin for 40 fins or more
Cross-Cutting
- Fins longer than 300mm require additional transverse cutting to suppress surface waviness
6.Cross-Cut Implementation
For extended fin configurations, the implementation of cross-cutting is advised to mitigate surface curvature deviations, suppress waviness formation, and enhance turbulent airflow dynamics.
7.Fin Removal for Component Clearance
To accommodate attachment hardware (e.g., fasteners or auxiliary components), machined features should be fabricated as square or rectangular geometries with radiused corner profiles. Clearance dimensions must correlate with the mechanical specifications of mating components (e.g., screw head diameter) to eliminate spatial interference risks. Final clearance parameters—including corner radii and dimensional tolerances—are determined through engineering analysis to guarantee manufacturability and milling precision. Post-machining, residual steps measuring approximately 0.2 mm will persist in fin-removal zones due to material subtraction during CNC operations.
WHY choose Customized Heat Sink?
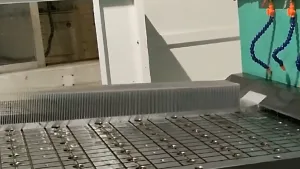
Custom Sizes Up to 3m x 90cm
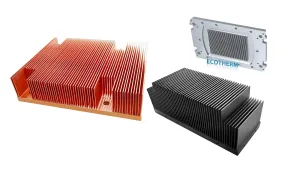
Specialized Surface Finishes
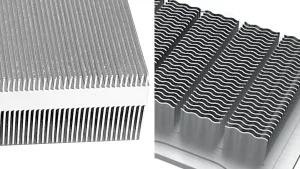
Double-Sided & Wavy Skived Fin Options
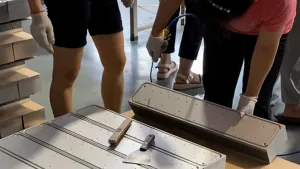
100% Quality Inspection
Explore Our Range of Tailored High-Power Designs
Customize for Unique Heat Sink Solutions
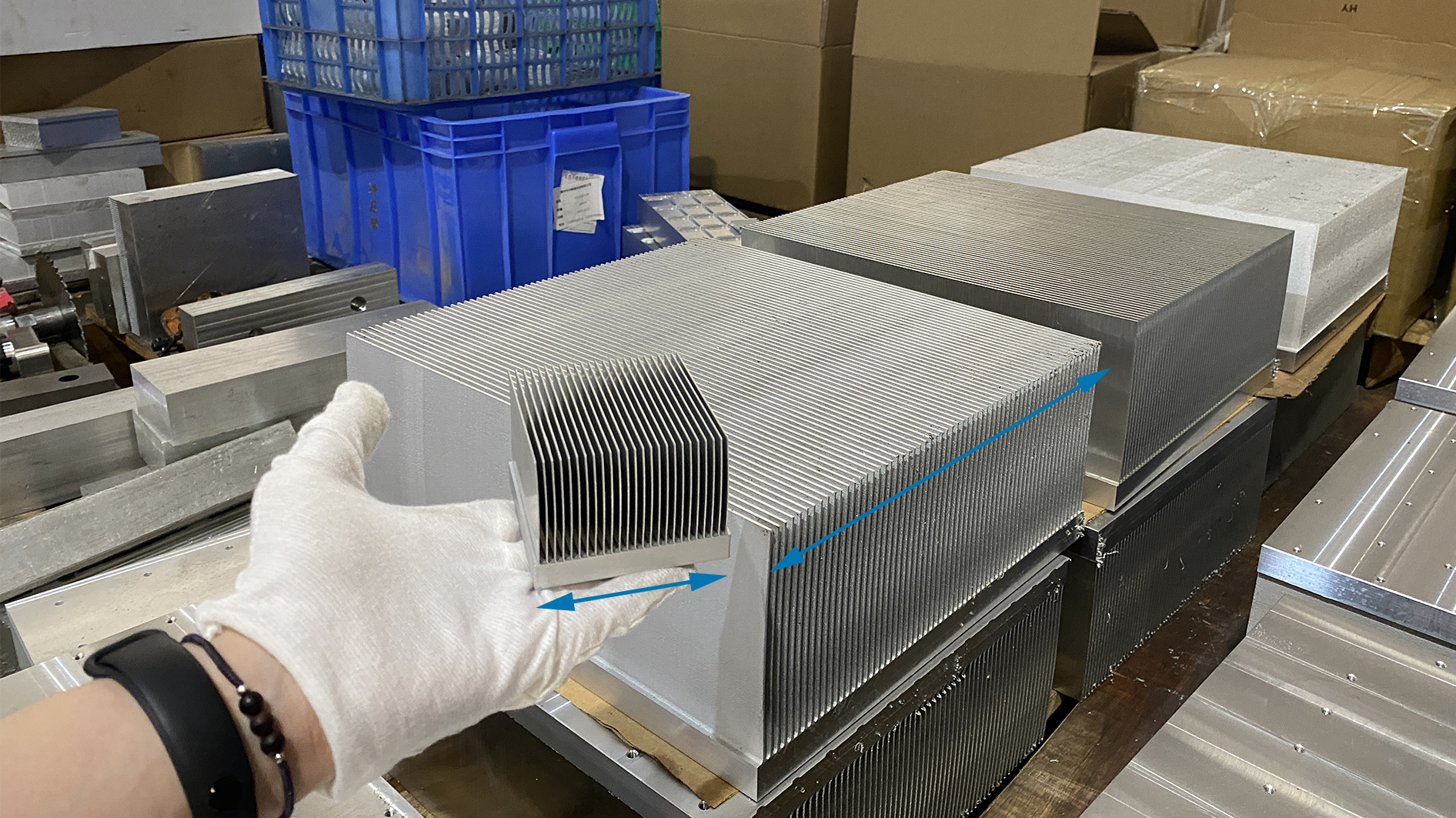
Dimension and Shape
Customers can specify the dimensions (length, width, height) and shape (e.g., rectangular, circular, or custom shapes) based on their application requirements.
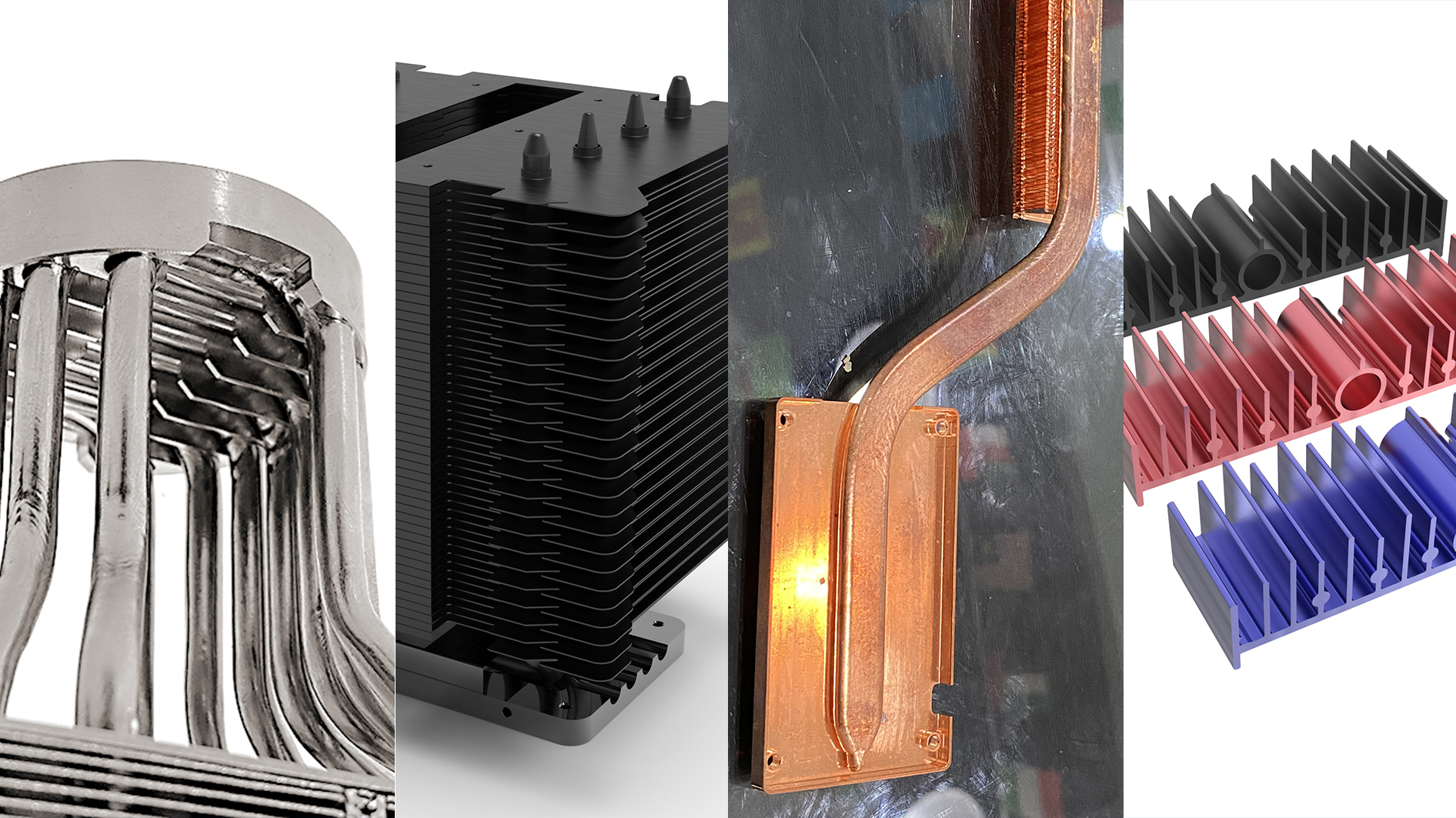
Surface Treatment
Options for different materials, such as aluminum, copper, or composite materials, can be provided to meet thermal conductivity, weight, and cost considerations.
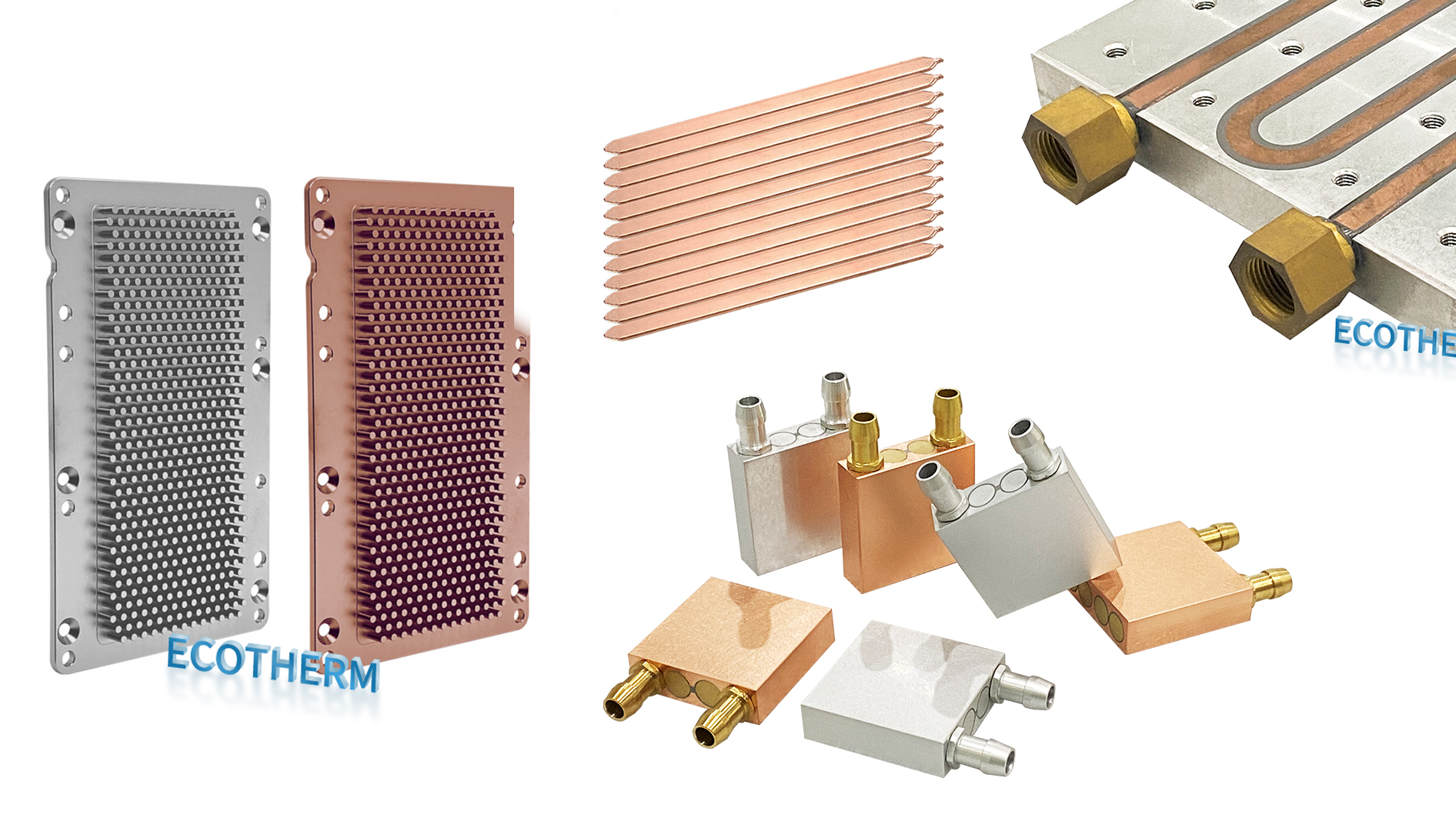
Material Selection
Various surface treatment options can be offered, such as anodizing, coating, or nickel plating, to enhance corrosion resistance and aesthetics.
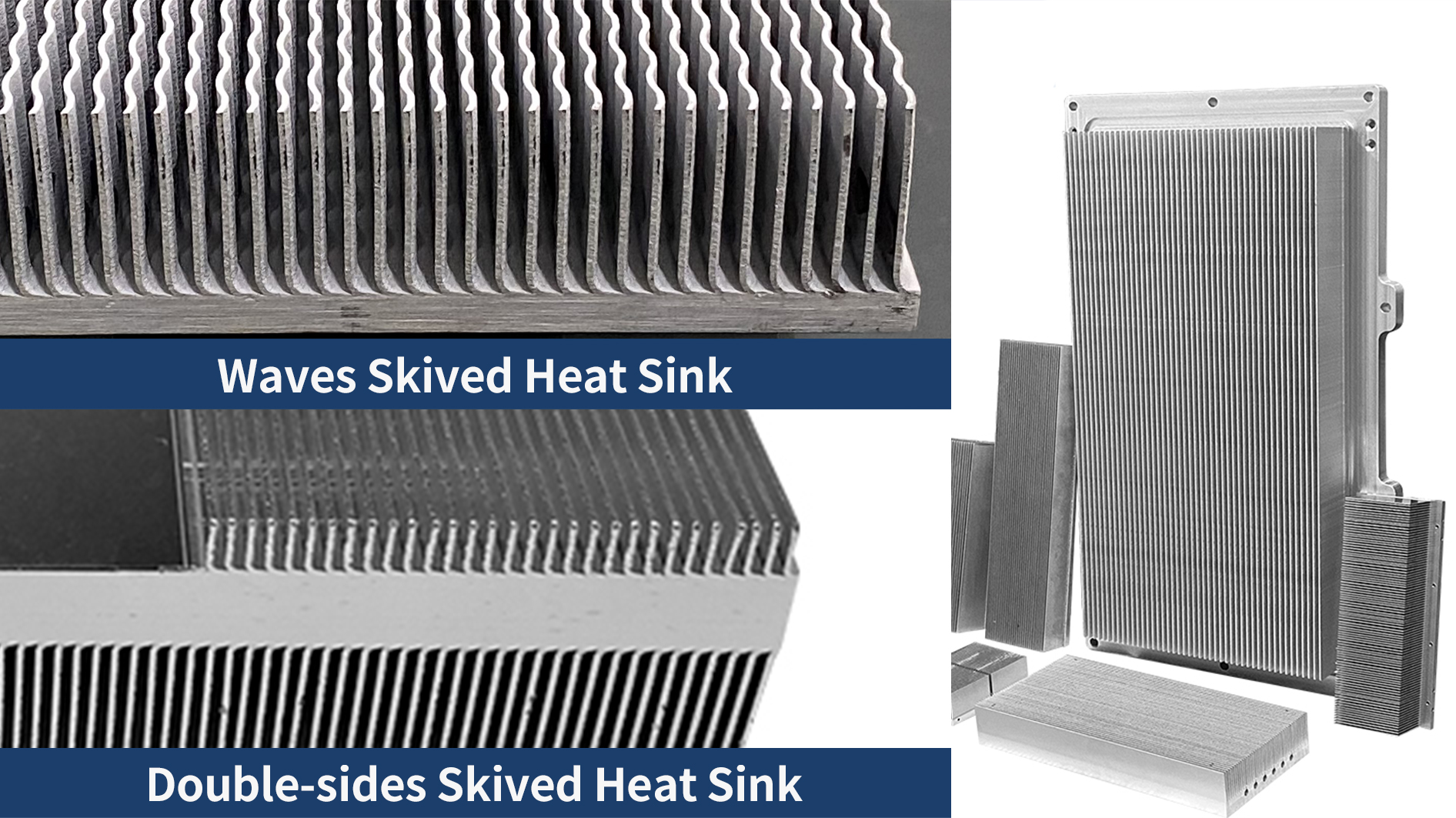
Thermal Performance
The design of the heat sink can be customized regarding the number and shape of fins to optimize heat transfer and dissipation efficiency.
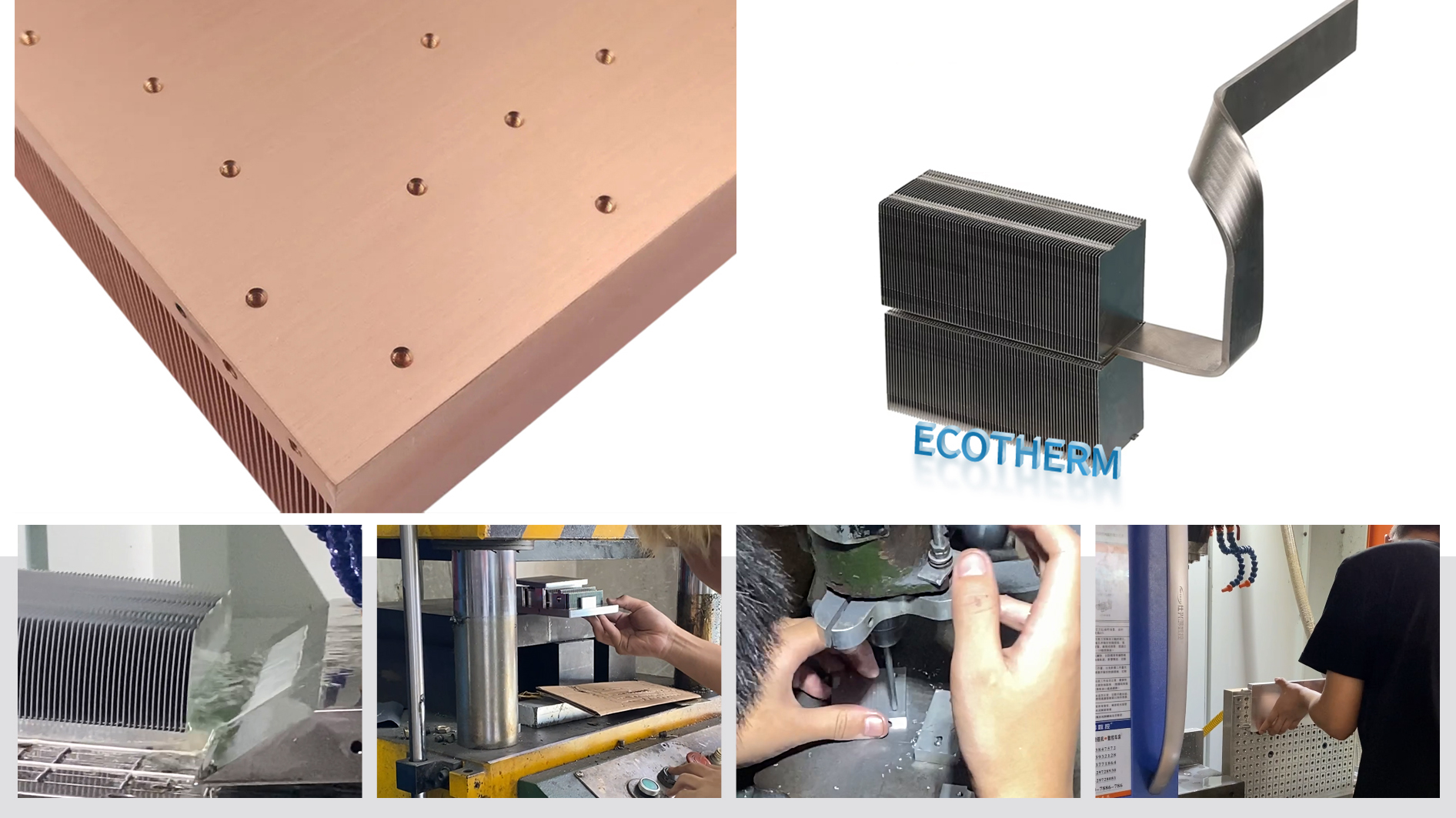
Mounting Options
Customization for mounting methods (such as screw mounting, clamps, or welding) and interface design can be provided to fit specific installation requirements.
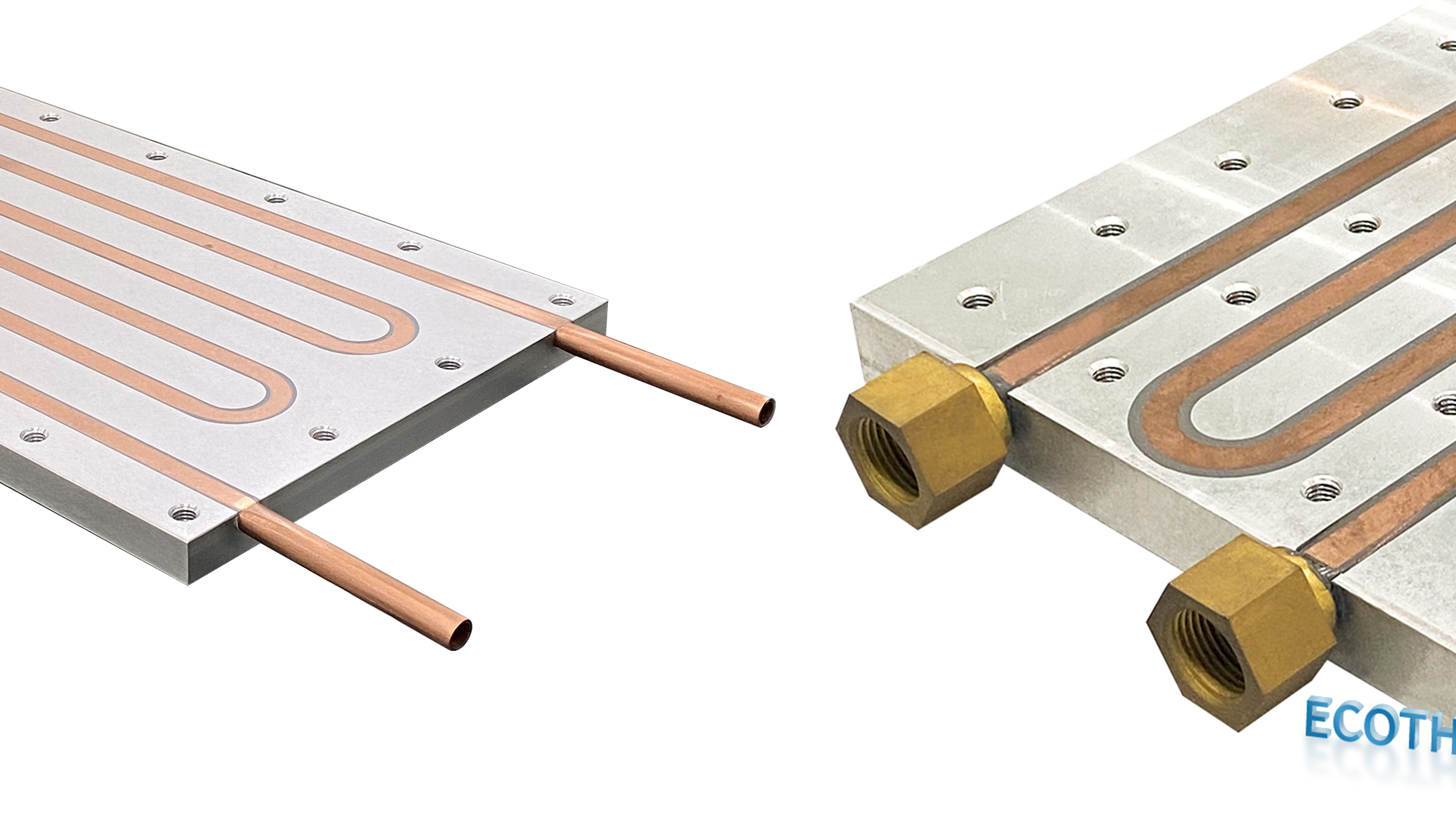
Additional Features
Options for integrating additional functionalities, such as fan incorporation, temperature sensor placement, or fluid cooling channels, can enhance the thermal management capabilities.
Choose Another Type of Heat Sink
Custom designs for every unique need.
Crafting Custom
Heatsinks for Your Needs
Feel free to get in touch with us to discuss your project specifics, request quotes, or inquire about our capabilities.
Our team of experts is dedicated to delivering top-notch quality and precision in every heatsink we produce
Free 24 Hours Feedback Thermal Analysis
Focus On Customized Cooling Solutions
22 Years Experiences OEM Factory
Send Your Drawing For Evaluation
CONTACT ECOTHERM
Please contact us to get in touch with our experts. We can provide design services for your project and thermal simulation services within 24 hours.
Note: Ecotherm does not provide a standard thermal model.We focus on providing professional design and production services for your new projects