Factors Driving the Manufacturing Cost of Liquid Cold Plates
The two biggest cost drivers in cold plate manufacturing are thermal conductivity requirements and annual demand, which are typically out of the control of thermal engineers and manufacturing engineers. However, you can reduce costs by understanding how factors such as roughness, flatness, hardness, surface topology, mounting features, and liquid connection specifications influence the cost of the liquid cold plate. By involving cold plate manufacturers early in the design process, you can identify manufacturing cost drivers and select the most cost-effective design.
Most cold plates are made from aluminum, although some newer technologies use copper. While copper offers better thermal conductivity, aluminum is more commonly used because it is generally cheaper, lighter, and easier to work with. Copper machining is very difficult and expensive. Currently, the two most popular aluminum cold plate technologies are tubular and vacuum brazed (see Figure 1). Tubular cold plates typically consist of copper or stainless steel tubes pressed into grooves in aluminum extrusions. They offer excellent cost advantages and provide good heat dissipation for medium to low power density devices. Vacuum brazed cold plates are composed of two plates metallurgically bonded together with internal fins. They come in a variety of sizes and offer extremely high performance, making them ideal for applications with concentrated heat loads. Both tubular and vacuum brazed water cooling heat sinks have time limitations in their manufacturing processes.
After the factors mentioned above, the largest cost driver for aluminum cold plates is machining time and additional processing steps. Cold plate manufacturers often have costs associated with machining time, including machine usage, power, consumables, and depreciation on maintenance. Therefore, the longer a water cooling plate is in the manufacturing equipment, the higher the cost. Each additional processing step further drives up the cost.
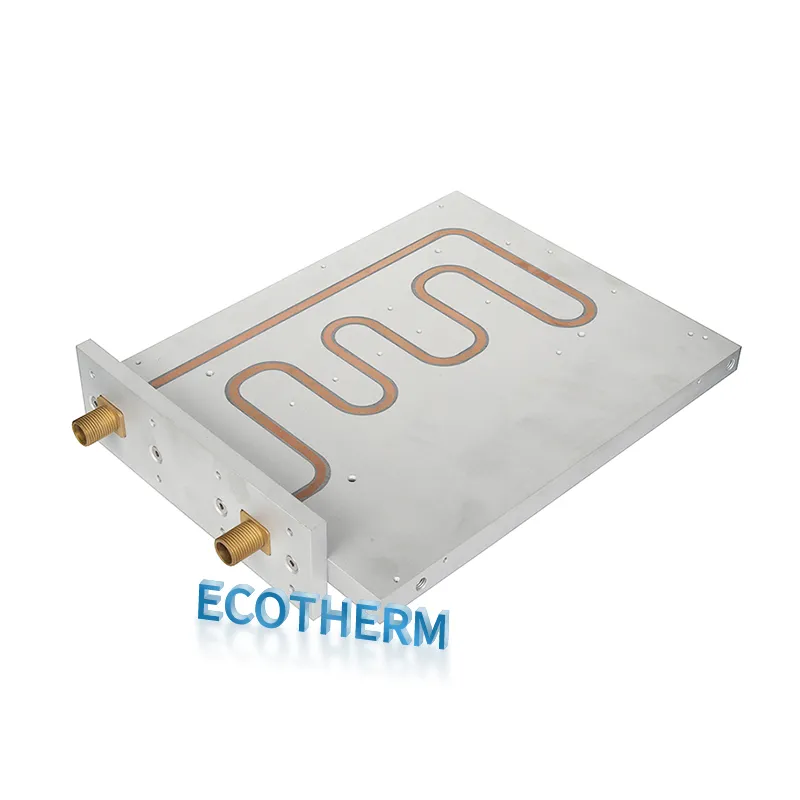
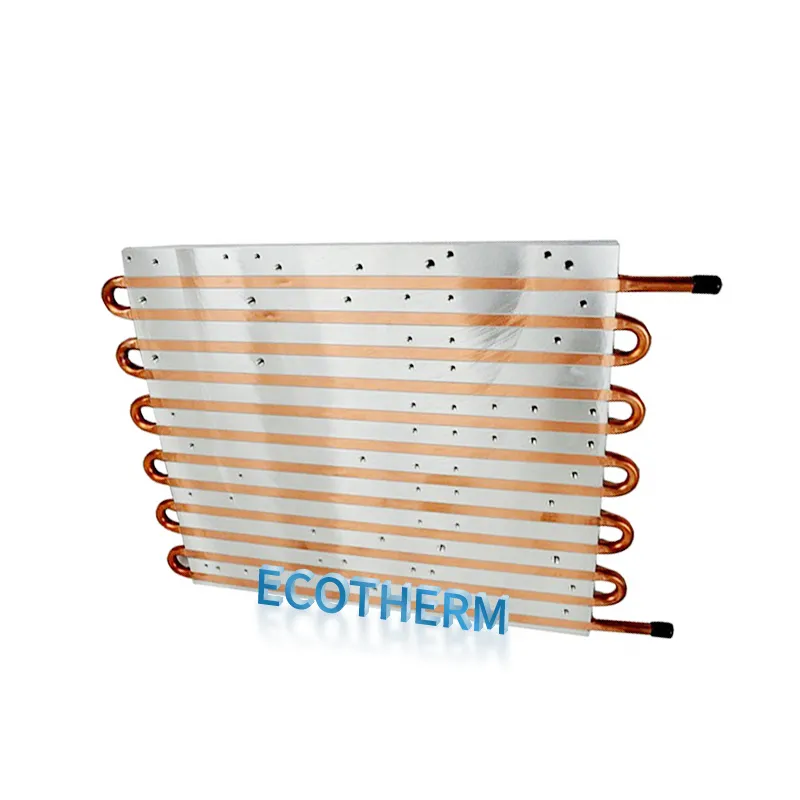
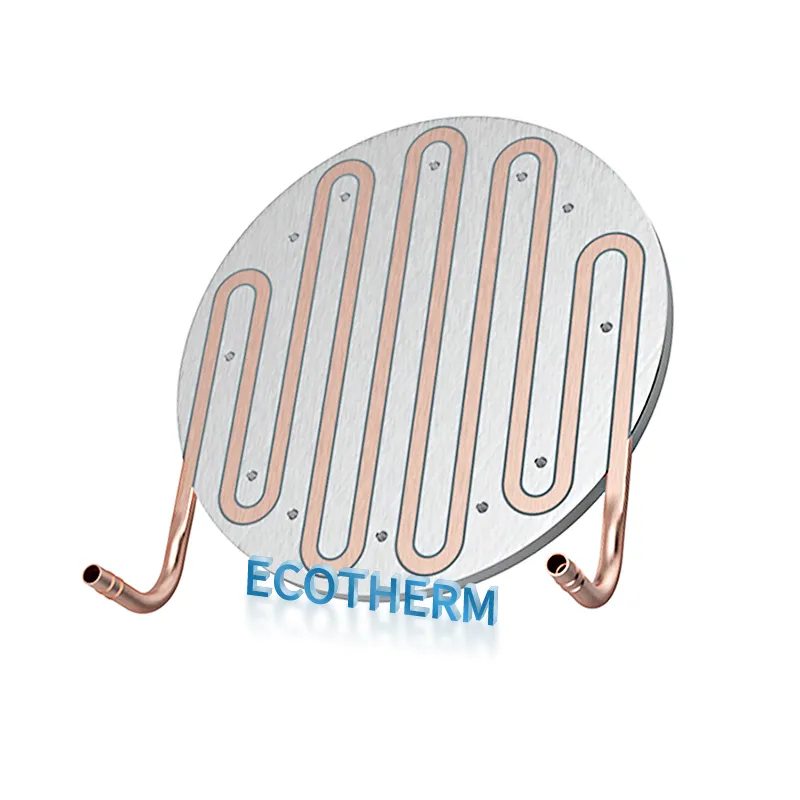
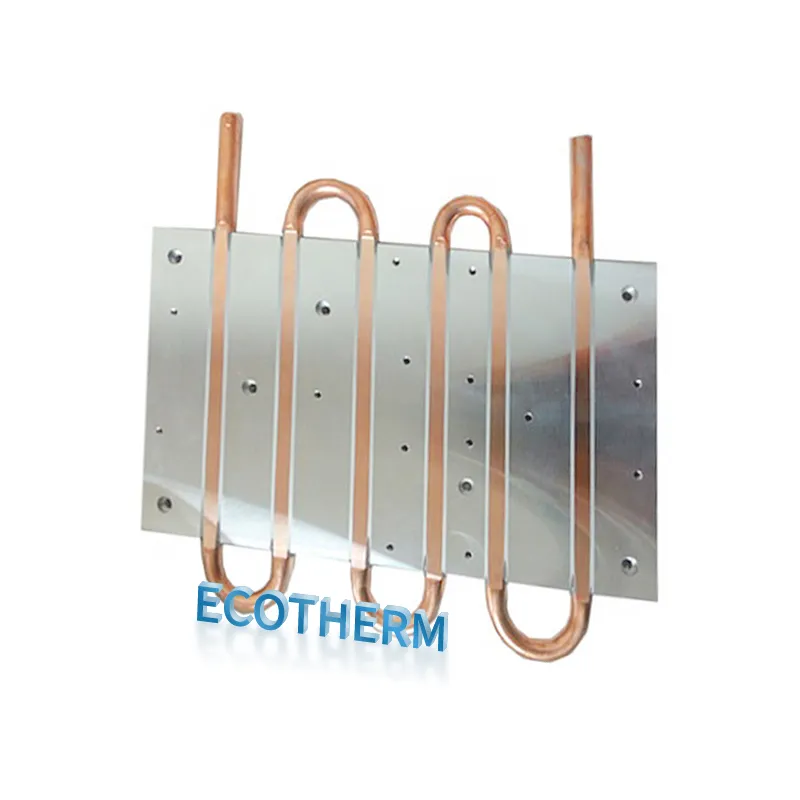
(1) Extrusions and Die-Casting
To minimize machining time and reduce costs, it is best to utilize extrusions and casting as much as possible. Extrusion is the process of forcing metal through a mold to create an object with a fixed cross-section. Molds for new extrusions are relatively inexpensive, with extrusion dimensions typically limited to about 9 inches (22.86 cm) in width. The wall thickness of extrusions needs to be relatively consistent, and any channels or features must be straight. Manufacturers can also combine extrusion with machining to lower costs. Some features can be extruded, while more complex features can be machined afterward. This will help reduce extrusion costs, provided you design the plate with extrusion features in mind. Another option is combining casting and machining to manufacture cold plates. For example, if a casting is not flat enough, secondary operations are needed to meet the flatness specifications of the custom heat sink. Extrusion or casting usually requires a high minimum order quantity, so you need the correct application to justify the use of these processes. Both extrusion and casting can save a significant amount of cost at scale.
(2) Surface Roughness
Surface roughness (or finish) can significantly increase costs with minimal impact on performance. Contrary to some beliefs, roughness has a relatively small effect on the thermal performance of liquid cold plates. In most applications, the surface contact between the cold plate and components is less than 10%, with the remaining 90% consisting of air gaps. A smoother surface will only slightly reduce the percentage of air gaps. The typical surface finish for machined cold plates is 32-64 μin (81-163 μcm), which is sufficient for most applications. Using standard machining centers can reduce roughness to 16 μin (41 μcm), but this requires sturdier fixtures to minimize any potential vibration, as well as slower spindle speeds and feed rates. Slower speeds and feeds mean longer machining times, which increases costs.
In most applications, thermal interface materials (TIM) are used between components or circuit boards and water cooling plates to help reduce gaps. TIM should be as thin as possible since its relatively high thermal resistance masks any conductivity improvements achieved with smoother surfaces. Increasing the clamping force of components or boards on the cold plate also helps offset higher roughness, although it can introduce additional stress on the plate or components. As the cold plate and components heat up, clamping stress also increases the impact of coefficient of thermal expansion (CTE) mismatch.
(3) Surface Flatness
Surface flatness has a much greater impact on the thermal performance of cold plates than surface roughness because if the cold plate is not flat, the contact area is greatly reduced (see Figure 2). The standard flatness specification is 0.001 inches/inch (0.003 cm/cm). This means that, within a one-inch measurement span, the lowest point on the cold plate should not be more than 0.001 inches (0.003 cm) lower than the highest point. If a flatter flatness is required, one cost-saving method is to specify local flatness rather than requiring the entire plate to be flat. For example, if multiple Insulated Gate Bipolar Transistors (IGBTs) are to be installed on the cold plate, and each IGBT requires 0.001 inches/inch (0.003 cm/cm) flatness across the entire substrate, it would be better to specify local flatness for each individual IGBT location instead of demanding that the entire plate be perfectly flat.
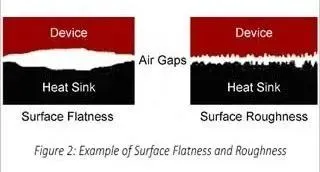
(4) Layout Design
Minimizing surface topology is also crucial for cost reduction, especially for circuit board applications. Complex surface topologies usually require starting with a thick aluminum block and then machining away the excess material. This increases the cost of raw materials and extends machining time. If topology cannot be avoided, bundling similar components together on the circuit board can help reduce machining requirements.
(5) Hardness
Cold plates made from casting, extrusion, or vacuum brazing are very soft after processing, typically having a T0 hardness. Cold plates need to be hardened because soft aluminum is difficult to machine and handle. To achieve a hardness from T0 to T4, the cold plate must undergo heat treatment. The heat treatment process involves heating the cold plate to 1000°F (538°C) and holding it at that temperature for about 1 hour per inch of cold plate thickness, followed by rapid cooling to induce thermal shock (see Figure 3). One way to cool the cold plate is to drop it directly from the furnace into a water bath. To go from T4 to T6, the cold plate must undergo artificial aging. This is achieved by placing the cold plate in a 300°F-400°F (149°C-204°C) environment for 8-16 hours. T6 offers very high tensile strength, which is typical for military and aerospace applications. However, for most applications, T4 is sufficiently hard, and specifying T6 would unnecessarily increase costs.
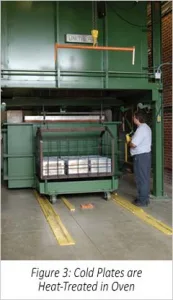
(6) Mounting Features/Holes
An additional cost-driving factor in cold plate manufacturing is the number of holes. A hole can add up to $3 to the cost of a cold plate. The main reason holes increase costs is that they cannot be placed in the fluid path. For tubular cold plates, bending the pipes to accommodate holes is necessary, and each bend increases the cost. For vacuum brazed cold plates, islands must be created in the fluid path, which also means electrical discharge machining (EDM) of the internal fins. This adds significant machining time and increases costs.
Strict tolerances on hole locations and spacing also drive up costs. Reasonable tolerance specifications are ±0.005 inches (±0.013 cm). As with flatness, specifying local tolerances wherever possible will help reduce costs. For large cold plates where the holes are far apart, tolerances become harder to maintain. One reason is that machine tool tolerances increase with the distance the machine head moves. Another reason is that temperature gradients of up to 18°F (10°C) in the machining shop can cause the cold plate to expand or contract by up to 0.005 inches (±0.013 cm). Through-holes are the easiest to specify with stricter tolerances, as creating them requires only a single tool operation, while threaded holes are more difficult due to the need for two tools. Spiral oil holes are the hardest to tolerance since this process involves both tapping and spiral oiling, each with its own tolerance. All of these tolerances contribute to the difficulty and cost of manufacturing.
(7) Liquid Connections
For liquid connections, straight-thread O-ring ports generally work best. They offer the best seal at the lowest cost, aside from welded systems. Pipe connections (such as NPT fittings) cannot provide the precision required for components like liquid cold plates. For vacuum brazed cold plates, avoid using external threaded fittings such as kick-back or bead fittings, as these require additional operations (such as welding) to connect the fittings. Additionally, fittings that extend beyond the cold plate require protection during shipping, which could increase packaging costs. Quick-disconnect fittings should only be used when necessary, as each pair can cost as much as $750. Cold plates or electronics that require frequent disconnects benefit from these fittings. For cold plates that are already filled with coolant, they are also required.
Another consideration for liquid connections is port tolerance. Typically, incoming pipes have some flexibility. A reasonable tolerance is between ±0.030 inches (0.076 cm) and ±0.060 inches (0.152 cm).