Heat Sink Solutions:Liquid Cooling Heat Dissipation Technology
Development History
Early Exploration (1964):
In 1964, IBM first adopted cold plate liquid cooling (indirect contact heat dissipation) in its mainframe computer System 360. Heat was conducted through a metal cold plate to an external circulating coolant, marking the beginning of liquid cooling applications in the IT field.
Technical Dormancy and Revival (2008–2009):
- In 2008, IBM launched the liquid-cooled supercomputer Power575.
- In 2009, Intel introduced a mineral oil immersion system, verifying the feasibility of liquid cooling in data centers.
Rapid Development Phase:
In recent years, with the continuous increase in chip power and power density of ICT equipment in data centers, as well as the explosion of artificial intelligence application demands, liquid cooling technology has entered a period of rapid growth.
Current Development Status
Technical Routes:
- Single-Phase Cold Plate:
The coolant is in liquid state, typically water-based (e.g., deionized water, ethylene glycol aqueous solution). This is the most widely used method, as it generally does not affect the rack architecture or infrastructure of data centers. - Two-Phase Cold Plate:
The coolant exists in both liquid and gas states within the cold plate module, enhancing heat dissipation capacity through latent heat of phase change. However, it requires higher system airtightness and more complex equipment and system maintenance. - Single-Phase Immersion:
ICT equipment is submerged in dielectric coolants (typically fluorinated liquids or oils) for heat dissipation. This includes Tank single-phase immersion, node single-phase immersion, and node spray immersion. - Two-Phase Immersion:
Uses two-phase dielectric coolants to remove chip heat through latent heat of vaporization, offering strong heat dissipation capabilities. However, it presents design challenges and is relatively expensive.
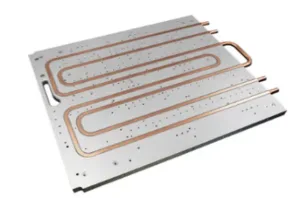
Market Applications
Data Centers:
Cold plate liquid cooling dominates the data center liquid cooling market with approximately 90% share due to its high maturity and low operational complexity. However, as single rack power continues to increase, the application of immersion liquid cooling is expected to gradually rise.
Other Fields:
In supercomputing and high-performance computing, fully immersive liquid-cooled servers are becoming a future technical trend. NVIDIA has also stated that all future GPU products will transition to “liquid cooling” for heat dissipation.
Future Trends
Technical Optimization Directions:
- Enhanced Heat Dissipation: As chip power increases, liquid cooling technologies will continuously optimize to provide stronger heat dissipation capabilities and meet the cooling demands of next-generation ICT equipment chips. Two-phase cold plate and two-phase immersion solutions may gradually gain advantages.
- Improved Reliability: Single-phase cold plate solutions will further enhance reliability and reduce leakage risks; immersion liquid cooling will continue to advance in coolant compatibility, supporting equipment (e.g., CDU), and standardization of data center-level solutions to improve overall reliability.
Market Development Trends:
- Market Size Growth: According to IDC, the Chinese liquid-cooled server market is expected to achieve a compound annual growth rate (CAGR) of 54.7% from 2022 to 2027, with a market size of $8.9 billion by 2027.
- Material Innovation: Development of coolants and cold plate materials with higher thermal conductivity and lower costs.
- Increased Standardization: Establishment and improvement of industry standards will be a key direction for future liquid cooling technology development, enhancing compatibility between products, reducing costs, promoting popularization and application of liquid cooling, and facilitating large-scale industry growth.
- Expanded Application Scenarios: Beyond data centers, supercomputing, and high-performance computing, liquid cooling technology will be widely adopted in artificial intelligence, 5G communications, electric vehicles, and other fields.
- Intelligentization: Integration with IoT and AI technologies to achieve intelligent monitoring and optimization of liquid cooling systems.
- Green and Environmentally Friendly: Promotion of eco-friendly coolants to reduce environmental impact.
- Cost Reduction: With technological advancements and mass production, the cost of liquid cooling technology will further decrease.
>>>Heat Sink Solutions: Scaling for Data Centers and Chip Evolution
>>>Heat Sink Solutions:Development of Data Centers
>>>Heat Sink Solutions:Vapor Chamber (VC) Cooling Technology
>>>Heat Sink Solutions:3D VC (Three-dimensional two-phase Homogeneous Temperature technology)
>>>Heat Sink Solutions:Liquid cooling heat dissipation technology
>>>Heat Sink Solutions:Other Cooling Technologies (Diamond and Graphene Cooling)
>>>Heat Sink Solutions:Heat Dissipation Path and Development Route of Thermal Interface Materials