Heat Sink Structural Design
1.Natural Convection Heat Sink Design
The design of the heat sink can start with the envelope volume, and then detailed design can be done on parts like fins and the base dimensions.
- Envelope Volume
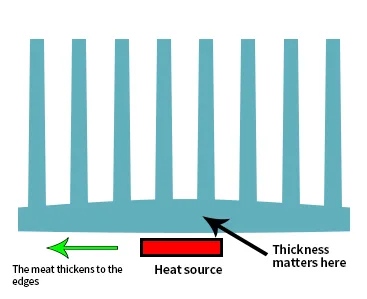
Base Thickness of the Heat Sink
A good base thickness design should be thick at the heat source part and gradually become thinner toward the edge. This allows the heat sink to absorb enough heat from the heat source and quickly transfer it to the thinner parts of the heat sink.
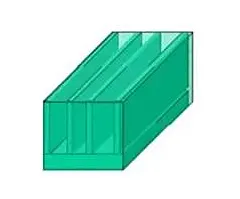
Relationship between base thickness and input power.
2.Fin Shape
The air layer thickness is approximately 2mm, and the spacing between fins needs to be more than 4mm to ensure smooth natural convection. However, this may reduce the number of fins, which reduces the surface area of the heat sink.
A. Narrower Fin Spacing
Decreases natural convection, reducing heat dissipation efficiency.
B. Wider Fin Spacing
Reduces the number of fins, decreasing surface area.
Fin Angle
The fin angle is approximately 3 degrees.
Fin shape reference values.
3.Fin Thickness
When the shape of the fins is fixed, the balance between thickness and height becomes important. Particularly, if the fin is thin and tall, it will cause heat transfer difficulties at the front end. This results in the heat sink not being able to improve efficiency even with an increased volume.
Thinner Fins
Reduces the heat transfer capacity to the top.
Thicker Fins
Reduces the number of fins (decreasing surface area).
Taller Fins
Reduces heat transfer capacity to the top (decreasing volumetric efficiency).
Shorter Fins
Reduces surface area.
4.Heat Sink Surface Treatment
Surface treatment such as acid-resistant anodized aluminum (Alumite) or anodic treatment can enhance radiation performance and improve the heat dissipation efficiency of the heat sink. Generally, color (whether white or black) has little impact.
Surface protrusions can increase the heat dissipation area, but in natural convection conditions, they may obstruct the air layer, reducing efficiency.