Liquid Cooling Thermal Management in IGBT
Liquid Cooling Technology
When the IGBT operates in a high-frequency state, heat loss causes a continuous increase in the module’s temperature, which severely affects the performance of IGBT power semiconductor devices.
At the same time, the reliability of the components decreases, significantly reducing their lifespan. More than half of IGBT device failures are caused by thermal faults, so thermal management is critical. This issue becomes even more significant when the power of the equipment is very high (in the megavolt-ampere range), where conditions such as duct design, wind pressure supply, and noise levels make implementation extremely difficult.
Traditional forced air cooling technologies can no longer adequately meet the heat dissipation requirements of the equipment. Water cooling, with its superior cooling capacity, is more suitable for use in the heat dissipation systems of high-power IGBT power semiconductor devices. As a result, water cooling technology is gradually being more widely adopted.
Currently, water cooling technology has become very mature.
Research has been conducted on the design of water cooling systems for high-power IGBT modules.
Through simulations and engineering experiments, the challenges of IGBT cooling system parameter design have been addressed.
A thermal resistance solving formula for the thermal paths of water cooling systems, based on similarity theory, has been proposed.
Additionally, methods for designing the first and second cooling structure parameters have been developed. Jiang Kun and others studied direct water-cooling IGBT power module finned-pin heat sinks. Through finite element simulation analysis, they summarized the effects of key parameters on heat dissipation performance and confirmed the optimal performance of the finned-pin heat sink in terms of fin diameter, fin spacing, fin length, and flow rate.
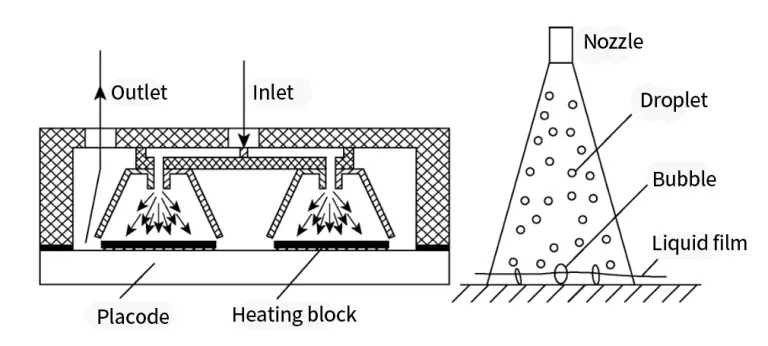
Figure 1 Liquid Jet Cooling
Direct cooling technology also includes jet cooling heat dissipation. Navodo explored the jet cooling method, as shown in Figure 1, which uses jet streams to impact the surface of the heated module. The results showed that increasing the droplet diameter can enhance the heat transfer coefficient.
Oliphant and others conducted experimental comparative studies on the heat transfer performance of spray cooling and jet cooling, as shown in Figure 2. Spray cooling utilizes high pressure to atomize the liquid and spray it onto the heated surface to achieve cooling. The results indicated that spray cooling provides better heat transfer performance.
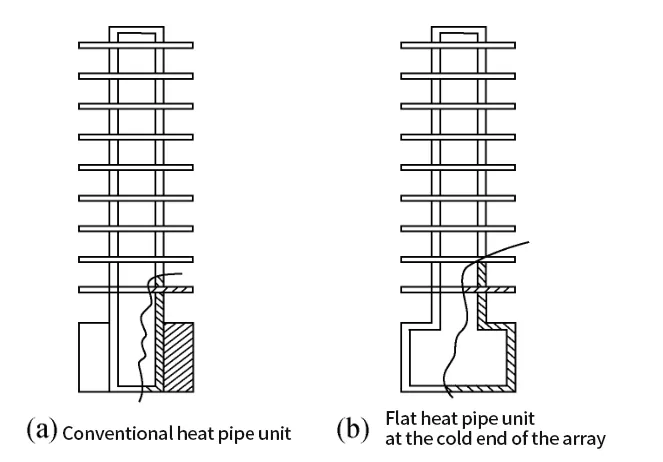
Figure 2 Liquid Spray Cooling
In liquid cooling systems, the power module comes into direct contact with the coolant, eliminating contact thermal resistance and providing better uniform temperature distribution.
Research shows that the heat dissipation capacity of direct liquid cooling can reach 800W/cm².
Generally, liquid cooling can be divided into indirect and direct liquid cooling based on whether they use copper substrates.
Studies indicate that heat dissipation structures without copper substrates can effectively reduce the overall thermal resistance of the heat dissipation module by 20% to 40%. This is mainly because removing the copper substrate also eliminates the thermal conductive silicone grease layer.
While this silicone grease layer is thin, it has a very low thermal conductivity, which is extremely detrimental to heat dissipation and generates significant thermal resistance. Therefore, most current liquid cooling heat dissipation structures use direct liquid cooling solutions without copper substrates.
IGBT power semiconductor modules, as the core components of current power electronic devices, are significantly affected by accumulated heat, which severely impacts their safety, reliability, and performance. As heat dissipation issues become more prominent, the cooling requirements for modules are becoming increasingly stringent.
To meet the development of IGBT power semiconductor devices toward higher power and higher integration, existing technologies such as finned heat sinks, air cooling, liquid cooling, traditional heat pipe cooling, and PCM-based heat sinks have become relatively mature. However, considering their heat transfer performance, operational reliability, and system costs, phase-change cooling, forced liquid cooling, and micro-cooling technologies have become current hot topics in heat dissipation research.
This article focuses on the latest developments in finned heat sinks, air cooling, liquid cooling, heat pipes, and phase-change heat dissipation technologies.
Considering all system factors, the most suitable technology for IGBT power semiconductor heat dissipation is optimized heat pipe technology that combines traditional heat pipe principles and structures.
One important future direction will be research into enhancing heat transfer performance and optimizing the structure.