Several Efficient Heat Dissipation Methods for Electronic Products
Heat dissipation design
Natural heat dissipation or cooling method
Natural cooling is a very commonly used heat dissipation method. Natural cooling is a cooling method that utilizes the high thermal conductivity of materials (mainly referring to profiles) to carry away heat and dissipate it into the air.
That is, in the absence of specific wind speed requirements, natural convection heat sinks such as copper-aluminum heat dissipation plates, extruded aluminum heat sinks, machined heat sinks or alloy heat dissipation castings are used to achieve the heat dissipation of products.
The natural heat dissipation and cooling method is mainly applied to electronic components with relatively low requirements for temperature control, low-power equipment and components in which the heat flux density of the heat generated by the devices is relatively low.
Forced heat dissipation
The forced heat dissipation or cooling method is a way to accelerate the air flow around electronic components through means such as fans and take away the heat.
Air cooling for heat dissipation is also a very common heat dissipation technology.
Its manufacturing is relatively simple, and it has the advantages of relatively low cost, simple installation, etc.
If there is a large space in electronic components to allow air flow or some heat dissipation facilities can be installed, this method can be applied. In practice, appropriately increasing the total heat dissipation area and generating a relatively large convective heat transfer coefficient on the heat dissipation surface are the main ways to enhance this convective heat transfer capacity.
Liquid cooling
Active refrigeration for heat dissipation
The methods of heat dissipation or cooling through refrigeration mainly include two types: the phase change cooling of the refrigerant and Peltier refrigeration. Different methods are adopted in different environments, and they should be applied reasonably according to the actual situation.
01 Phase change cooling of the refrigerant
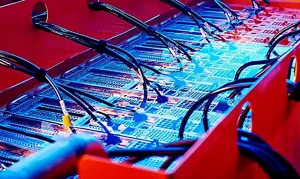
02 Semiconductor refrigeration
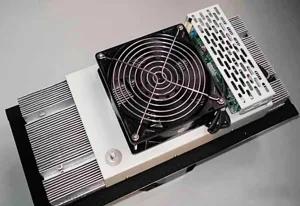
Heat conduction for heat dissipation
Thermal isolation heat dissipation method