Custom Heat Sink:The Impact of Heat Dissipation on High-Brightness LED
Compared to traditional fluorescent or incandescent lights, LED lighting offers higher energy efficiency. LED lighting is characterized by low power consumption, high brightness, and long lifespan, which effectively reduces energy consumption and conserves electricity resources.
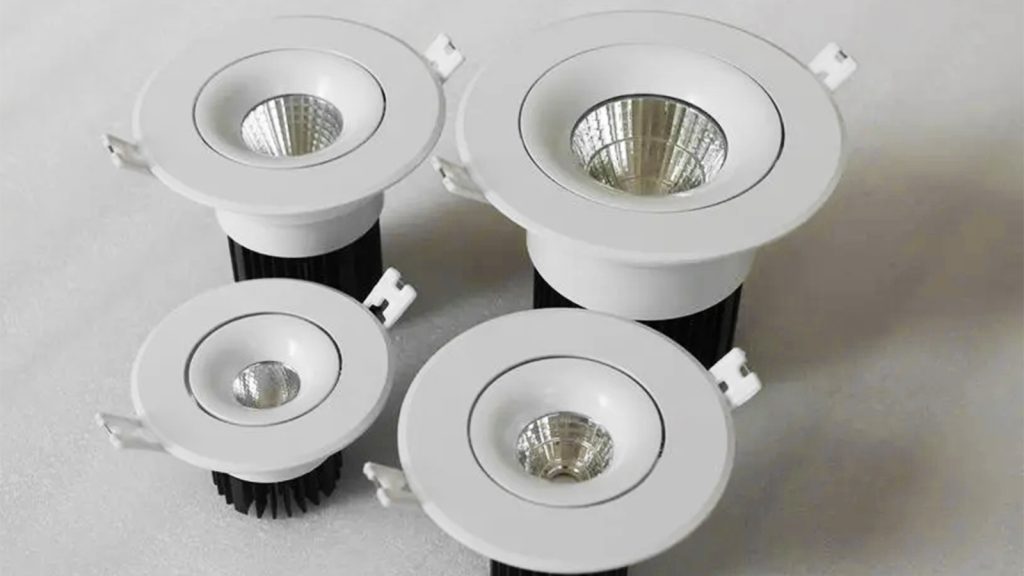
Working Principle of LEDs
LED stands for Light Emitting Diode, a semiconductor-based light-emitting material. With advancements in semiconductor research, large-scale LEDs have found widespread applications. LEDs are known for their low energy consumption, high brightness, long lifespan, and the ability to design them in various sizes for different applications like indoor decoration, automotive lighting, road lighting, and city illumination.
In practical use, LEDs cannot achieve 100% power efficiency; approximately 80% of input power is converted into heat. As large-scale, matrix-type LED lights are used more extensively, energy consumption also increases. Failure to address heat dissipation issues in a timely manner can lead to heat concentration at the LED’s PN junction, reducing its lifespan and potentially causing damage.
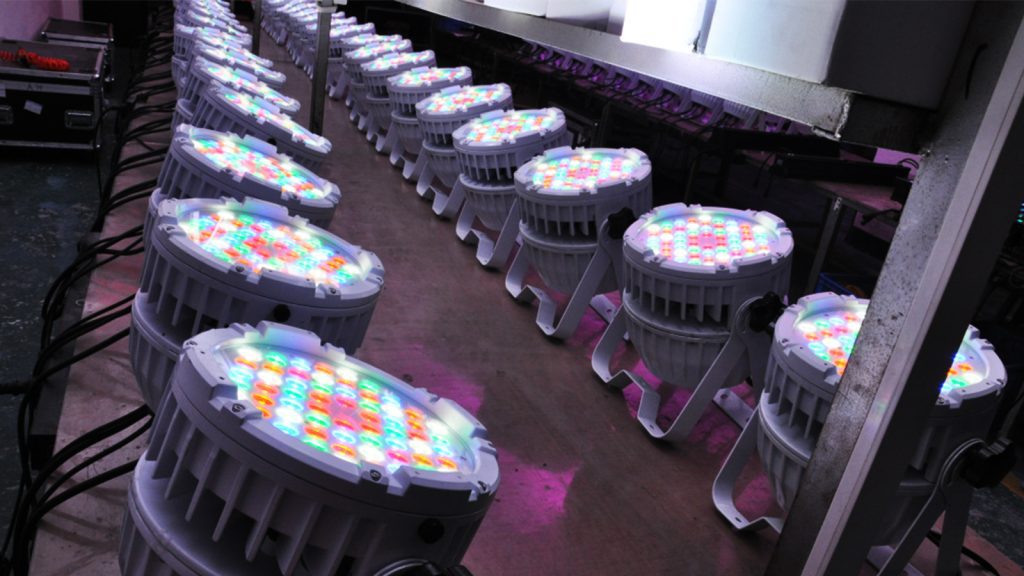
Heat Dissipation Challenges in LED Fixtures
LED fixtures, built around LED light sources, consist of LEDs, heat dissipation structures, drivers, and lenses.
Heat dissipation is a crucial factor affecting the illumination intensity of LED fixtures. The stability and quality of LED lighting are closely tied to the fixture’s heat dissipation.
For high-power LEDs, effective heat management is vital. Without proper heat dissipation, the internal temperature of LEDs increases, degrading LED performance and reducing its lifespan.
The most critical aspect of LED cooling is the heat path from the LED junction to the external part of the fixture. Heat needs to be conducted away from the LED efficiently and then removed from that area through cooling or heat dissipation.
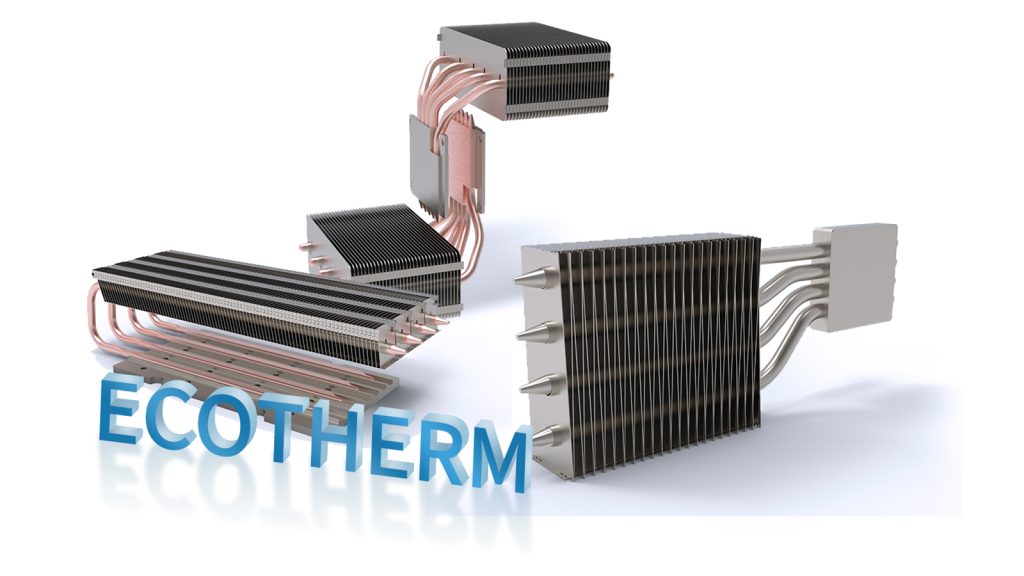
Types of Heat Dissipation
Heat dissipation can be categorized into passive and active methods.
Passive Heat Dissipation:
This method does not require external energy or devices and relies on natural heat transfer mechanisms, such as conduction and natural convection. Passive heat dissipation in LED fixtures typically involves using heat sinks, baseplates, and materials or structures that enhance heat transfer through increased surface area, airflow, or natural convection.
Active Heat Dissipation:
Active heat dissipation requires external energy or devices to aid in cooling. Examples include fans, liquid cooling, heat pipes, and semiconductor or chemical cooling methods. Active methods provide more control over heat dissipation but come with additional costs and energy consumption.
Heat Dissipation Techniques
1. Air Cooling:
Air cooling is the most common and cost-effective heat dissipation method. It relies on air convection to remove heat and is divided into natural convection (passive) and forced convection (active) techniques. While cost-effective, air cooling is sensitive to environmental conditions and can be affected by temperature increases and overclocking.
2. Choice of Heat Sink Material:
Heat transfer coeffcient(unit:W/mk) | |
Copper | 401 |
Aluminum | 237 |
Gold | 317 |
Silver | 42 |
Silver has the best thermal conductivity, but it is expensive. Currently, heat sinks are primarily made of aluminum and copper.
Common heat sink materials include copper, aluminum, and aluminum alloys. Copper offers excellent thermal conductivity but is expensive and heavier, while aluminum is cheaper and has good thermal conductivity. Most heat sinks use aluminum due to its cost-effectiveness and ease of processing.
3. Liquid Cooling:
Liquid cooling uses a fluid, typically deionized water, as a heat transfer medium to dissipate heat from the heat source to a cooling system. Liquid cooling provides higher efficiency, lower noise, and lower environmental dependence but comes at a higher cost.
4. Heat Pipe Cooling:
LED heat pipe cooling is a method of dissipating heat from LED fixtures using heat pipe technology. The heat pipe cooling system consists of a heat pipe, a heat sink, and a heat dissipation fan (optional). Heat pipe cooling efficiently transfers the heat generated inside the LED fixture to the heat sink using the principle of phase change.
In an LED heat pipe cooling system, the heat pipe serves as the heat transfer medium. When the LED chip generates heat, the working medium inside the heat pipe is heated and vaporized, and the vapor quickly transfers to the heat sink end through the capillary structure inside the heat pipe. It then condenses back into a liquid, releasing heat. Through this cycle, efficient LED heat dissipation is achieved.
The heat sink is used to dissipate the heat generated inside the LED fixture, reducing the LED’s temperature. Heat sinks are typically made of metal materials and have good heat dissipation performance with a large surface area. In some LED applications that require higher heat dissipation capabilities, heat sinks can be used in conjunction with heat dissipation fans. Heat dissipation fans accelerate airflow over the heat sink’s surface, further enhancing heat dissipation efficiency.
Compared to traditional air cooling, LED heat pipe cooling offers advantages such as high efficiency, low noise, high reliability, and flexible installation. It is suitable for LED applications that require high power density, quiet operation, and high reliability, making it a valuable heat dissipation technology.
Heat pipe cooling relies on a heat pipe to transfer heat rapidly from the LED to a heat sink. It utilizes the phase-change principle for efficient heat dissipation. Heat pipes are suitable for high-power-density and high-reliability LED applications.
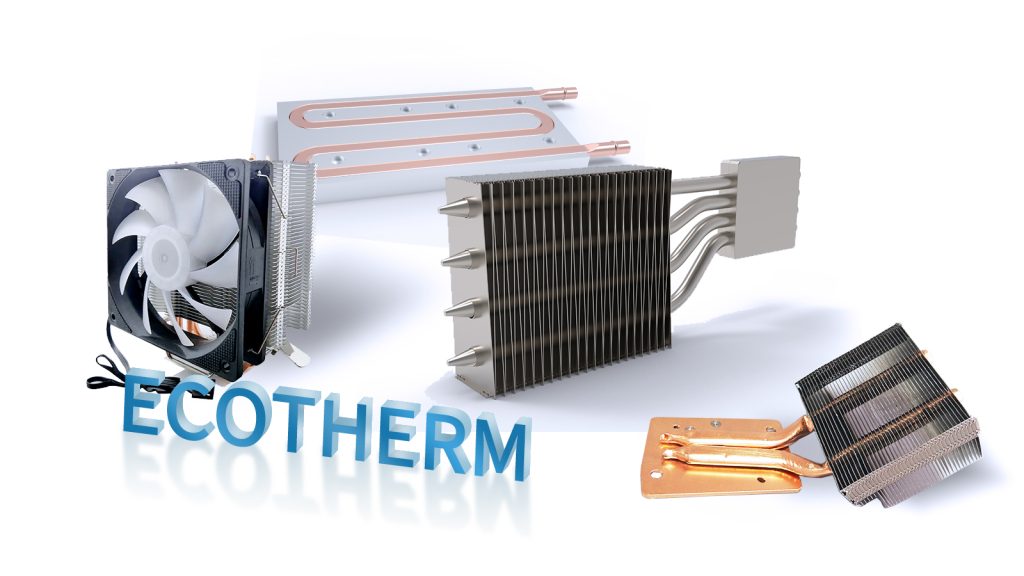
Heat Sink Design
Designing the heat sink is a crucial aspect of LED module design. Factors to consider include the heat sink’s form, shape, and whether it requires a fan.
Common heat sink fabrication techniques include Stamping, Extrusion, Forging, Copper-aluminum combination, Heat pipe modules, and Water cooling plates.
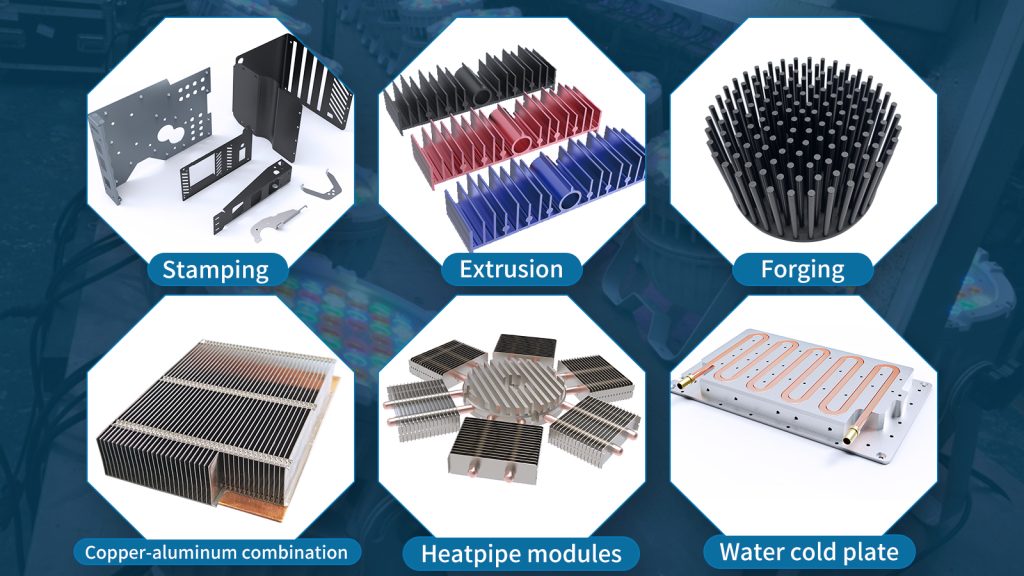
The choice of heat sink depends on the LED’s power requirements, with high-power LEDs typically using forging, copper-aluminum combinations, heat pipe modules, or water cooling plates.
The following is a common heat sink (skived heat sink):
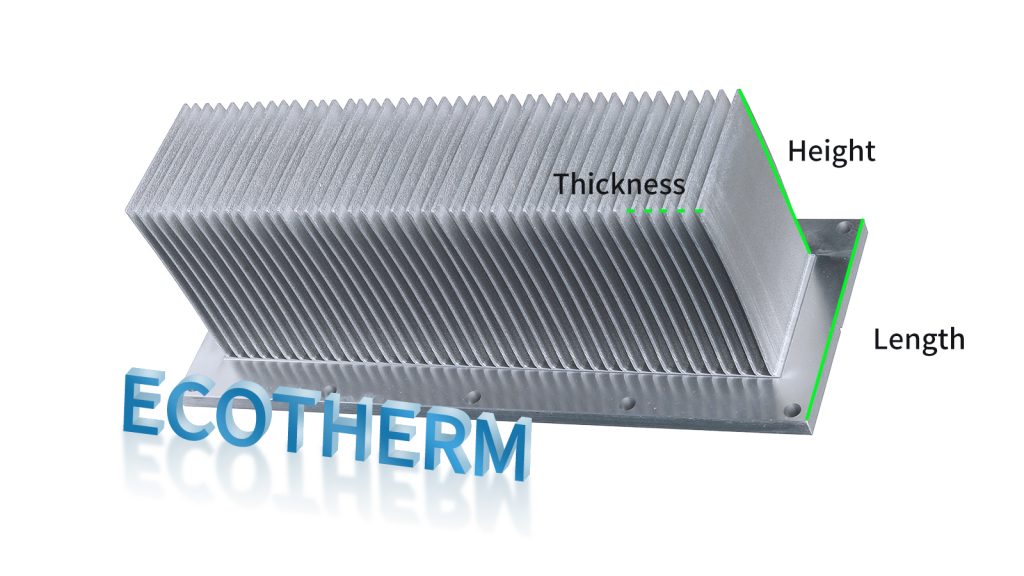
The skived heat sink features numerous fins, which effectively increase the heat dissipation surface area. The height, width, and thickness of the fins all impact the heat dissipation performance of the fins.
In conclusion, heat dissipation is a critical factor for high-brightness LEDs. While LEDs offer advantages like energy efficiency, low power consumption, high brightness, and long lifespan, they also generate significant heat during operation. Proper heat dissipation is essential to maintain LED performance and longevity. Heat dissipation methods can be passive or active, each with its advantages and considerations. Selecting the appropriate heat dissipation technique and heat sink design is crucial to ensure stable LED operation and extended lifespan.
At Ecotherm, we offer customized heat dissipation solutions tailored to your specific needs, whether for industrial lighting, outdoor lighting, or special applications. Please feel free to contact us for efficient heat sink solutions for your project.