Exploring Stamping Parts Heat Sinks for Precise Cooling
Forging Heat Sink: An Efficient and Versatile Cooling Solution
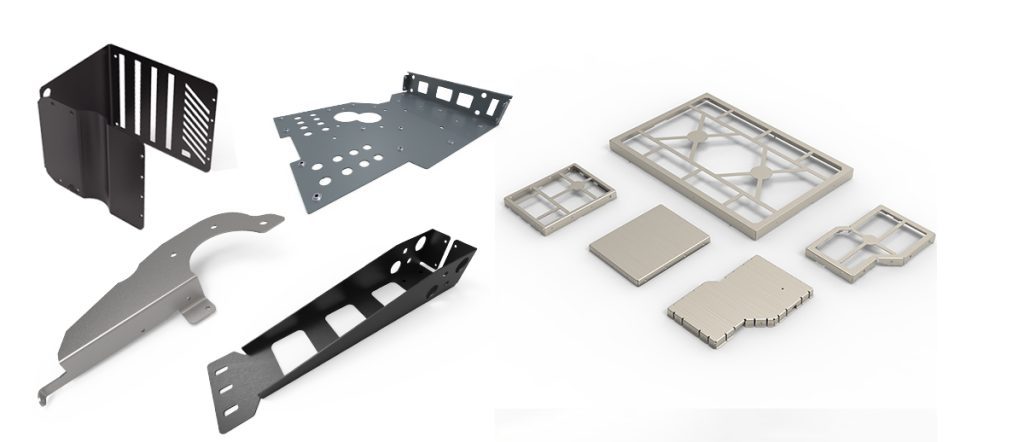
Cold forging is a remarkable alternative to casting for creating intricate shapes with superior thermal conductivity in heat sinks. This process ensures the production of nearly perfect straight fins, allowing for a higher number of fins per square millimeter. Cold forged heat sinks come in various shapes, including plate fin, round pin, and elliptical fin configurations, each tailored to suit specific cooling requirements.
One of the key advantages of cold forging is its compatibility with copper, as it doesn’t require high temperatures for shaping, minimizing damage to the material. Additionally, secondary machining operations such as hole drilling, chamfering, and step creation can be seamlessly integrated during the cold forging process, reducing material wastage and optimizing manufacturing efficiency.
Forged heat sinks, a modification of the cold forging process, are meticulously crafted using high pressure and low temperature to eliminate air bubbles and impurities, resulting in improved thermal properties and increased material density. Radian Thermal Products employs special open die tooling and intense pressure to produce high precision heat sinks with impressive aspect ratios.
The design versatility allows fins to be round, elliptical, straight, or any combination on a single part, catering to diverse application demands.
Another significant advantage lies in the versatility to manufacture forged heat sinks of the same design with varying heights using a single set of forging dies, enhancing production efficiency and adaptability to different specifications.
When dealing with high aspect ratios or dense fins, the absence of thermal interfaces between the fins and the base in forged heat sinks yields superior performance compared to stamped-fin or bonded-fin heat sinks.
To further optimize heat distribution in aluminum heat sinks, copper inserts can be embedded into the base during the forging process.
While this process may be relatively expensive, it proves beneficial for larger volumes where the cost can be efficiently distributed. For smaller volumes, an alternative worth exploring is extrusion with a cross-cut to produce square pins. For higher production volumes, die casting provides a cost-effective solution without compromising on quality.
In conclusion, the forging heat sink offers an efficient and versatile cooling solution for a wide range of electronic applications.
The cold forging process ensures excellent thermal conductivity and enables the creation of complex shapes with precision and density. With the ability to customize designs, work with various materials, and achieve high aspect ratios, forged heat sinks stand out as a reliable choice for effective thermal management in demanding electronic systems.